3D printing production method for automobile engine cylinder block
A technology of automobile engine and 3D printing, which is applied in casting molding equipment, metal processing equipment, casting mold composition, etc., can solve the problems of high trial production cost, complex core assembly method, and difficult control of product size, so as to save mold production cost, The effect of simplifying the molding process of core assembly and reducing the production cost of castings
- Summary
- Abstract
- Description
- Claims
- Application Information
AI Technical Summary
Problems solved by technology
Method used
Image
Examples
Embodiment Construction
[0025] Embodiments of the present invention are described in detail below. The embodiments described below are exemplary only for explaining the present invention and should not be construed as limiting the present invention. If no specific technique or condition is indicated in the examples, it shall be carried out according to the technique or condition described in the literature in this field or according to the product specification. The reagents or instruments used were not indicated by the manufacturer, and they were all commercially available conventional products.
[0026] The invention provides a 3D printing production method for an automobile engine cylinder block, including three parts: a pouring system design method, a sand core design method, and a core assembly molding method, specifically including the following steps:
[0027] (1) Gating system design: According to the design principle of the gating system, the middle pouring open gating system is adopted, th...
PUM
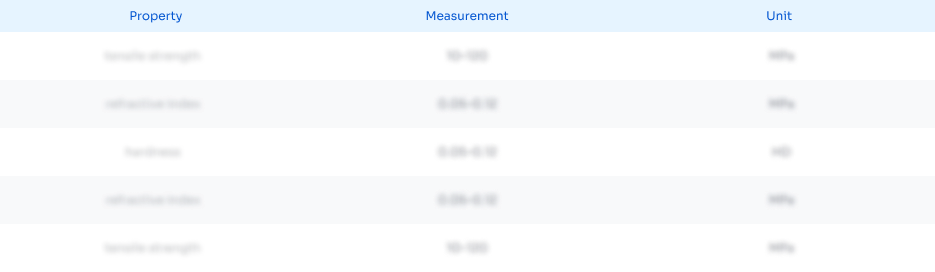
Abstract
Description
Claims
Application Information

- R&D
- Intellectual Property
- Life Sciences
- Materials
- Tech Scout
- Unparalleled Data Quality
- Higher Quality Content
- 60% Fewer Hallucinations
Browse by: Latest US Patents, China's latest patents, Technical Efficacy Thesaurus, Application Domain, Technology Topic, Popular Technical Reports.
© 2025 PatSnap. All rights reserved.Legal|Privacy policy|Modern Slavery Act Transparency Statement|Sitemap|About US| Contact US: help@patsnap.com