Turnover feeding system of capacitor fixing agent
A fixing agent, capacitor technology, applied in the direction of capacitors, capacitor manufacturing, circuits, etc., to achieve the effect of reasonable structure, improve production efficiency, and promote production development
- Summary
- Abstract
- Description
- Claims
- Application Information
AI Technical Summary
Problems solved by technology
Method used
Image
Examples
Embodiment
[0029] Such as figure 1 As shown, a capacitor fixing agent flip feeding system of the present invention includes a machine base 1, a guide shaft 2, a fixing agent storage flip assembly 3, a stepped guide shaft 4, a chain lifting assembly 5, a flip limit assembly 6, a limit Bit collar 7, top plate 8;
[0030] The base 1 is used for fixedly installing the guide shaft 2, the stepped guide shaft 4 and the chain lifting assembly 5;
[0031] The guide shaft 2 and the stepped guide shaft 4 are installed on the base 1 to play a guiding role;
[0032] Such as figure 2 As shown, the fixing agent storage turning assembly 3 is used to store the fixing agent, and is driven by the chain lifting assembly 5 to move up and down and flip and blank at the turning position; the fixing agent storage turning assembly 3 includes a linear bearing 301, a lifting plate 302, overturn bracket 303, hinge pin 304, overturn joint 305, storage box installation plate 306, rubber pad 307, fixative storage ...
PUM
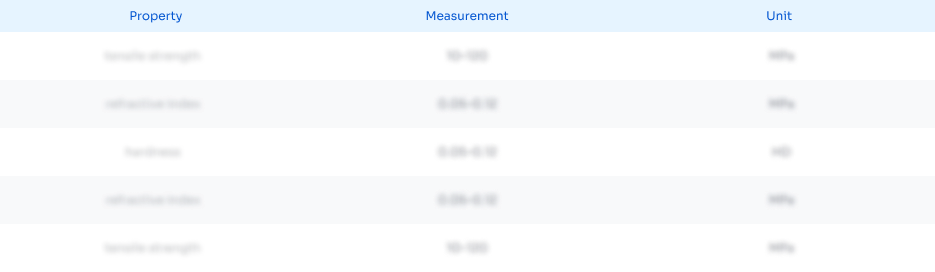
Abstract
Description
Claims
Application Information

- R&D Engineer
- R&D Manager
- IP Professional
- Industry Leading Data Capabilities
- Powerful AI technology
- Patent DNA Extraction
Browse by: Latest US Patents, China's latest patents, Technical Efficacy Thesaurus, Application Domain, Technology Topic, Popular Technical Reports.
© 2024 PatSnap. All rights reserved.Legal|Privacy policy|Modern Slavery Act Transparency Statement|Sitemap|About US| Contact US: help@patsnap.com