Modeling method for modal of double-drive feeding system of numerical control machine tool
A dual-drive feed, CNC machine tool technology, applied in general control systems, control/regulation systems, simulators, etc., can solve the problems of unsolvable mode shape equations of continuous systems, cumbersome finite element software simulation operations, etc. The operability, the modeling method is intuitive, and the effect of high efficiency
- Summary
- Abstract
- Description
- Claims
- Application Information
AI Technical Summary
Problems solved by technology
Method used
Image
Examples
Embodiment Construction
[0024] In order to illustrate the technical scheme and technical purpose of the present invention, the present invention will be further introduced below in conjunction with the accompanying drawings and specific embodiments.
[0025] combine figure 1 A schematic flow chart of the present invention, a dual-drive feed system modal modeling method for a CNC machine tool of the present invention, comprising the following steps:
[0026] Step 1. Determine the generalized coordinates of the system: determine the degrees of freedom of the system, and select generalized coordinates to describe the motion state of the system, and the number of coordinates is the same as the number of degrees of freedom.
[0027] combine figure 2 , taking the position of the center of gravity of the worktable in a static state as the coordinate origin, establish the O-XYZ main coordinate system, the positive direction of the X-axis is perpendicular to the guide rail, the positive direction of the Y-a...
PUM
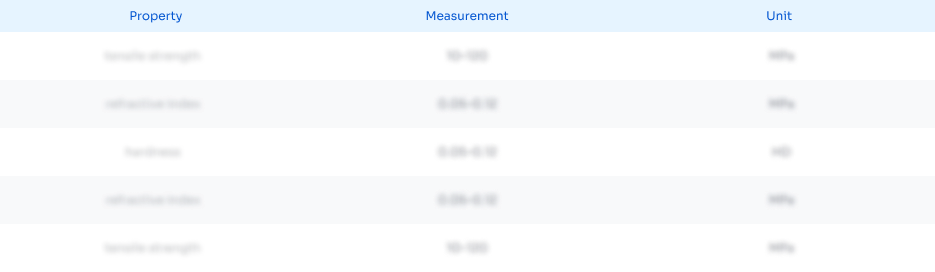
Abstract
Description
Claims
Application Information

- Generate Ideas
- Intellectual Property
- Life Sciences
- Materials
- Tech Scout
- Unparalleled Data Quality
- Higher Quality Content
- 60% Fewer Hallucinations
Browse by: Latest US Patents, China's latest patents, Technical Efficacy Thesaurus, Application Domain, Technology Topic, Popular Technical Reports.
© 2025 PatSnap. All rights reserved.Legal|Privacy policy|Modern Slavery Act Transparency Statement|Sitemap|About US| Contact US: help@patsnap.com