A Flexible Pneumatic Gripper with Force Feedback and Stroke
A technology of force feedback and pneumatic clamp, which is applied in the field of robotics, can solve problems such as object falling off, hidden safety hazards, and difficult control, and achieve the effect of enhancing self-adaptability, ensuring synchronization, and increasing the dimension of control
- Summary
- Abstract
- Description
- Claims
- Application Information
AI Technical Summary
Problems solved by technology
Method used
Image
Examples
Embodiment Construction
[0028] The specific implementation manners of the present invention will be further described in detail below in conjunction with the accompanying drawings and embodiments. The following examples are used to illustrate the present invention, but are not intended to limit the scope of the present invention.
[0029] see Figure 1-Figure 9 , a preferred embodiment of the present invention, the described flexible pneumatic gripper with force feedback and stroke includes a top shell 1, a timing belt unit 2, an intermediate air cavity 3, three sliders 4, and a tension sensor 5 and finger 6. Among them, there are two ports 1-1 connected with the air source on the top shell 1. The purpose of separating air inflation and air extraction here is to realize the self-locking function by using a one-way valve. Evenly distributed in the circumferential direction to form an equilateral triangle, the top shell 1 is provided with a chute 1-2, the slider 4 can slide towards or away from the c...
PUM
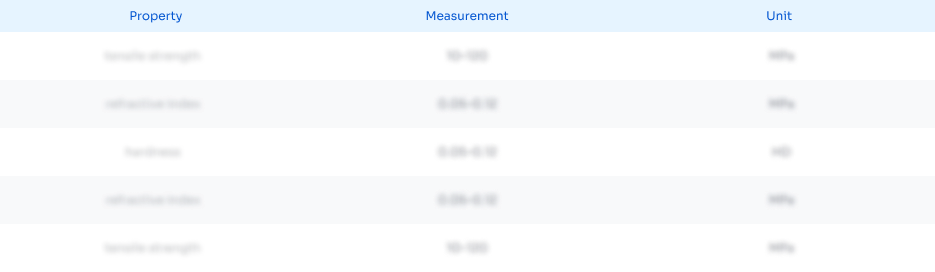
Abstract
Description
Claims
Application Information

- R&D
- Intellectual Property
- Life Sciences
- Materials
- Tech Scout
- Unparalleled Data Quality
- Higher Quality Content
- 60% Fewer Hallucinations
Browse by: Latest US Patents, China's latest patents, Technical Efficacy Thesaurus, Application Domain, Technology Topic, Popular Technical Reports.
© 2025 PatSnap. All rights reserved.Legal|Privacy policy|Modern Slavery Act Transparency Statement|Sitemap|About US| Contact US: help@patsnap.com