Welding manufacturing method of electron beam sleeved with large diameter T-shaped ring
A technology of electron beam welding and manufacturing method, which is applied to the field of electron beam welding manufacturing of large-diameter T-rings, which can solve the problems of difficulty in accurately guaranteeing dimensional accuracy, structural instability and damage, large welding deformation, etc.
- Summary
- Abstract
- Description
- Claims
- Application Information
AI Technical Summary
Problems solved by technology
Method used
Image
Examples
Embodiment 1
[0024] For a TC4 titanium alloy T-ring inner suit with a panel inner diameter of 1200mm, a width of 30mm, a thickness of 10mm, a rib height of 80mm, and a thickness of 10mm, the designed boss height is 2mm. Adjust the relative position of the panel and the rib, the assembly gap between the panel and the rib is less than 0.3mm, the axial misalignment is less than 0.2mm, fix it with the pressure plate and the clamping device; the vertical tolerance of the rib and the panel meets the requirements, less than 0.5mm, The outer diameter meets the requirements; the panel and the rib are spot welded, and the welding method is spot welding by manual argon tungsten arc welding. 0.2mm; Fix the assembled workpiece on the welding turntable and align it, put it into the vacuum chamber to evacuate, so that the vacuum degree reaches 5×10 -3 Weld the workpiece when it is below MPa; after vacuuming, start the electron beam welding machine, adjust the welding angle of the electron gun, so that th...
Embodiment 2
[0026] For the 40Cr steel T-ring inner suit with a panel inner diameter of 2800mm, a width of 35mm, a thickness of 20mm, a rib height of 75mm, and a thickness of 15mm, the designed boss height is 4mm. Before assembly, the residual magnetic content of the workpiece to be welded needs to be checked and demagnetized. Make the residual magnetic quantity≤1×10 -4 T; After the panel and the rib are assembled, put them on the welding platform and fix them, adjust the relative position of the panel and the rib. The device is fixed; the verticality tolerance of ribs and panels meets the requirements, less than 0.5mm, and the outer diameter meets the requirements; the panel and ribs are spot welded, and the welding method is spot welding by manual tungsten argon arc welding, and the spot welding points are evenly distributed At 8 positions of the weld to be welded, the assembly gap is uniform and stable, less than 0.2mm; fix the assembled workpiece on the welding turntable and align it, ...
PUM
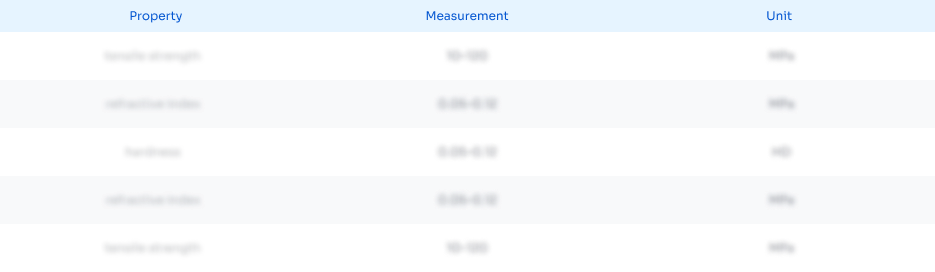
Abstract
Description
Claims
Application Information

- Generate Ideas
- Intellectual Property
- Life Sciences
- Materials
- Tech Scout
- Unparalleled Data Quality
- Higher Quality Content
- 60% Fewer Hallucinations
Browse by: Latest US Patents, China's latest patents, Technical Efficacy Thesaurus, Application Domain, Technology Topic, Popular Technical Reports.
© 2025 PatSnap. All rights reserved.Legal|Privacy policy|Modern Slavery Act Transparency Statement|Sitemap|About US| Contact US: help@patsnap.com