Satellite plate and shell structure-based finite element automatic modeling method
A technology of plate and shell structure and modeling method, which is applied in the field of aerospace, can solve the problems of low modeling efficiency, low level of knowledge integration and automation, irregular modeling process, etc., to reduce energy, improve product design performance, shorten The effect of the R&D cycle
- Summary
- Abstract
- Description
- Claims
- Application Information
AI Technical Summary
Problems solved by technology
Method used
Image
Examples
Embodiment Construction
[0038] A finite element automatic modeling method based on the satellite plate and shell structure of the present invention will be described in detail below in conjunction with the embodiments and drawings.
[0039] Such as figure 1 As shown, the present invention provides a finite element automatic modeling method based on the satellite shell structure, which specifically includes the following steps:
[0040] (1) Model import;
[0041] The user first establishes the model mapping information file and puts it in the work path; then starts the Patran software, specifies the set work path and file name; finally enters the location and name of the 3D design model to be analyzed. After submitting these information, the system will automatically complete the model import work.
[0042] The automatic modeling system is aimed at the characteristics of the satellite shell structure, using the mainstream finite element modeling software MSC.Patran in the domestic aerospace field as...
PUM
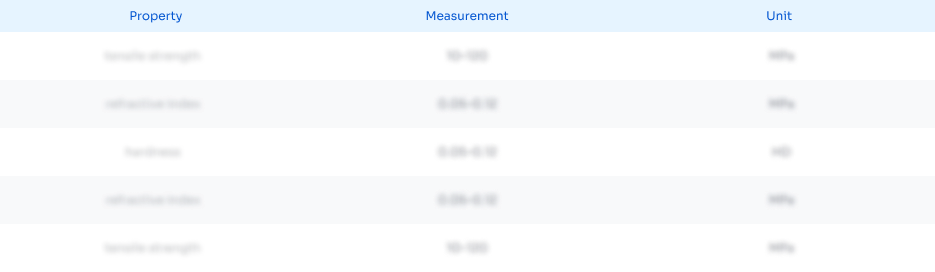
Abstract
Description
Claims
Application Information

- R&D
- Intellectual Property
- Life Sciences
- Materials
- Tech Scout
- Unparalleled Data Quality
- Higher Quality Content
- 60% Fewer Hallucinations
Browse by: Latest US Patents, China's latest patents, Technical Efficacy Thesaurus, Application Domain, Technology Topic, Popular Technical Reports.
© 2025 PatSnap. All rights reserved.Legal|Privacy policy|Modern Slavery Act Transparency Statement|Sitemap|About US| Contact US: help@patsnap.com