Switched reluctance motor current tracking control method, controller and speed adjusting system
A switched reluctance motor and current tracking technology, applied in the control system, vector control system, motor generator control and other directions, can solve the problem of ignoring the mutual inductance effect, improve the current tracking accuracy, the control method is simple and easy, and the reliability strong effect
- Summary
- Abstract
- Description
- Claims
- Application Information
AI Technical Summary
Problems solved by technology
Method used
Image
Examples
Embodiment 1
[0035] based on figure 1 with figure 2 In the simulink simulation model shown, the electrical equation of the k-th phase winding is:
[0036]
[0037] s(j) is the energization state of the k-th phase winding in the j-th control cycle, and the value is 1, -1 or 0, corresponding to the three states of positive pressure, negative pressure and zero voltage respectively. For 8 / 6 switching magnetic For a resistance motor, k represents any of the four phases of A, B, C, and D, and for a 6 / 4 switched reluctance motor, k represents any of the three phases of A, B, and C. Derived from equation (1), the current equation of the k-phase winding at time t is:
[0038]
[0039] Among them, θ is the rotor position angle at time t, U dc Is the bus voltage, L k (θ) is the average value of the inductance of the k-phase winding in the next control period T, R is the resistance value of the k-phase winding, and ω is the actual speed of the switched reluctance motor.
[0040] Such as image 3 As shown...
PUM
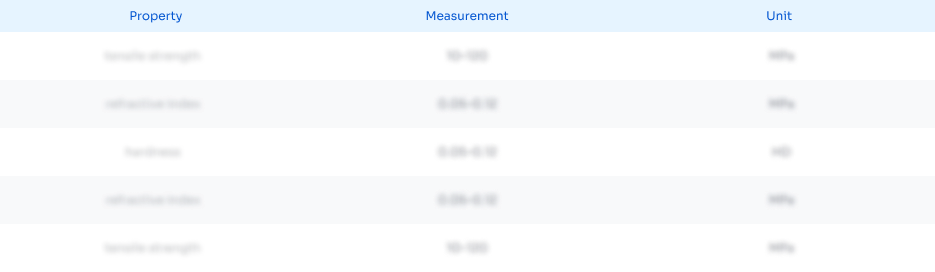
Abstract
Description
Claims
Application Information

- Generate Ideas
- Intellectual Property
- Life Sciences
- Materials
- Tech Scout
- Unparalleled Data Quality
- Higher Quality Content
- 60% Fewer Hallucinations
Browse by: Latest US Patents, China's latest patents, Technical Efficacy Thesaurus, Application Domain, Technology Topic, Popular Technical Reports.
© 2025 PatSnap. All rights reserved.Legal|Privacy policy|Modern Slavery Act Transparency Statement|Sitemap|About US| Contact US: help@patsnap.com