Mechanical arm error analysis method
An error analysis, robotic arm technology, applied in manipulators, claw arms, special data processing applications, etc., can solve the problems of low positioning accuracy and low working accuracy of robotic arms.
- Summary
- Abstract
- Description
- Claims
- Application Information
AI Technical Summary
Problems solved by technology
Method used
Image
Examples
Embodiment Construction
[0083] The present invention will be further described in detail below in conjunction with the accompanying drawings and embodiments.
[0084] Such as figure 1 Shown, in specific application examples, the detailed steps of the present invention are:
[0085] (1) Using the exponential product method to establish the kinematics model of the manipulator
[0086] select figure 2 The 6-DOF manipulator is shown as an example, which includes the initial configuration of the manipulator, link parameters, base coordinate system and tool coordinate system. The motion ranges of the six joints of the robotic arm are -180°~180°, -90°~90°, -90°~90°, -180°~180°, -90°~90°, -180°~ 180°. According to the definition of motion screw, according to the direction of each joint axis and the position where it passes through a point, the motion screw of each joint of the manipulator can be obtained as shown in Table 1:
[0087] Table 1 The motion screw of each joint of the manipulator
[0088] ...
PUM
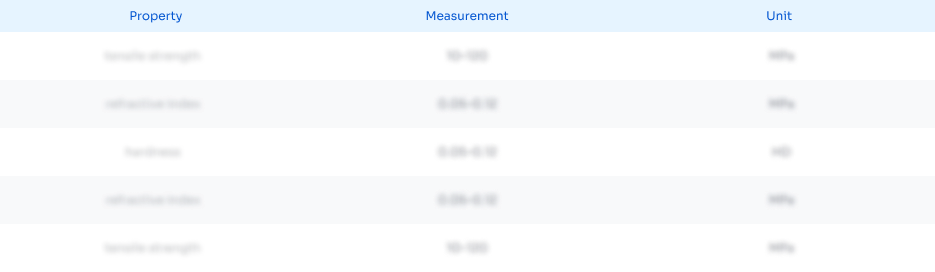
Abstract
Description
Claims
Application Information

- R&D Engineer
- R&D Manager
- IP Professional
- Industry Leading Data Capabilities
- Powerful AI technology
- Patent DNA Extraction
Browse by: Latest US Patents, China's latest patents, Technical Efficacy Thesaurus, Application Domain, Technology Topic, Popular Technical Reports.
© 2024 PatSnap. All rights reserved.Legal|Privacy policy|Modern Slavery Act Transparency Statement|Sitemap|About US| Contact US: help@patsnap.com