Fatigue life calculation method of welded steel bridge structure
A fatigue life and calculation method technology, applied in the calculation field, can solve problems such as economic losses and safety hazards of steel bridges, achieve good operability, wide application range, and overcome overestimation
- Summary
- Abstract
- Description
- Claims
- Application Information
AI Technical Summary
Problems solved by technology
Method used
Image
Examples
Embodiment Construction
[0041] see Figure 1 to Figure 3 , the fatigue life calculation method of a kind of welded steel bridge structure of the present embodiment, this method comprises the following steps:
[0042] S1: Establish a full-space S-N curve model of steel fatigue resistance considering average stress correction;
[0043] S2: Considering the coupling effect of welding residual stress and vehicle load stress, calculate the true stress time history of steel bridge welding details;
[0044] S3: Using the rainflow counting method to process the real stress time history, and calculate the stress amplitude, average stress and the number of stress cycles under a single traffic operation based on the processing results;
[0045] S4: Using the established full-space S-N curve model considering average stress correction, calculate the total number of stress cycles corresponding to the stress amplitude and average stress;
[0046] S5: Calculate the fatigue life of the welding details of the steel ...
PUM
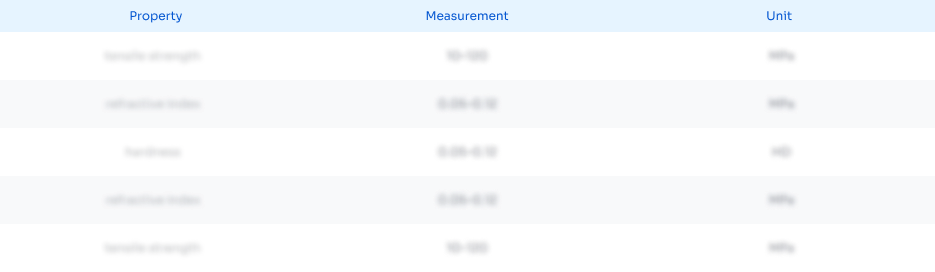
Abstract
Description
Claims
Application Information

- Generate Ideas
- Intellectual Property
- Life Sciences
- Materials
- Tech Scout
- Unparalleled Data Quality
- Higher Quality Content
- 60% Fewer Hallucinations
Browse by: Latest US Patents, China's latest patents, Technical Efficacy Thesaurus, Application Domain, Technology Topic, Popular Technical Reports.
© 2025 PatSnap. All rights reserved.Legal|Privacy policy|Modern Slavery Act Transparency Statement|Sitemap|About US| Contact US: help@patsnap.com