Method for segmental gathering, waste-heat utilization and SOx-NOx emission reduction of iron ore sintering flue gas
A sintering flue gas and enrichment technology, applied in the field of iron ore sintering, can solve the problems of low sensible heat utilization rate of sintered ore and high cost of flue gas purification, and achieve the effect of strong applicability and reduced operating costs
- Summary
- Abstract
- Description
- Claims
- Application Information
AI Technical Summary
Problems solved by technology
Method used
Image
Examples
Embodiment
[0054] Take a steel 210m 2 Taking the sintering machine as an example, there are 27 bellows in total, and the flue gas concentration is shown in Table 1.
[0055] Mix the flue gas from No. 1-16 sintered bellows 2 into flue 3 in the denitration section, and mix the flue gas from No. 17-27 sintered bellows 2 into flue 4 in the desulfurization section. The flue gas volume in flue 3 in the denitrification section is 177,000 Nm 3 / h, temperature 78℃, SO 2 Concentration 83mg / Nm 3 , NO x Concentration 183mg / Nm 3 ; The flue gas volume of the flue 4 in the desulfurization section is 149,000 Nm 3 / h, temperature 260℃, SO 2 Concentration 727mg / Nm 3 , NO x Concentration 25mg / Nm 3 .
[0056] The flue gas in the flue 3 of the denitrification section is exchanged with the sintered ore through the vertical cooler 7, and the temperature of the desulfurized tail gas after the heat exchange is above 350°C, and the dust is removed by the electrostatic precipitator to make the dust concen...
PUM
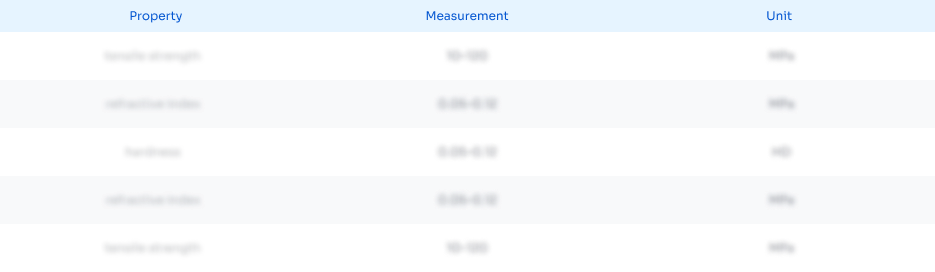
Abstract
Description
Claims
Application Information

- R&D
- Intellectual Property
- Life Sciences
- Materials
- Tech Scout
- Unparalleled Data Quality
- Higher Quality Content
- 60% Fewer Hallucinations
Browse by: Latest US Patents, China's latest patents, Technical Efficacy Thesaurus, Application Domain, Technology Topic, Popular Technical Reports.
© 2025 PatSnap. All rights reserved.Legal|Privacy policy|Modern Slavery Act Transparency Statement|Sitemap|About US| Contact US: help@patsnap.com