Modified conjugated diene polymer and tire rubber composition using same
A technology of conjugated dienes and polymers, which can be used in special tires, tire parts, transportation and packaging, etc., and can solve problems such as difficulty in use
- Summary
- Abstract
- Description
- Claims
- Application Information
AI Technical Summary
Problems solved by technology
Method used
Image
Examples
Embodiment 1
[0063] 1) Manufacture of linear SBR
[0064] Put 170g of styrene, 630g of 1,3-butadiene, and 4150g of hexane into a 10L autoclave reactor, add 10ml of tetramethylethylenediamine (TMEDA), and raise the temperature of the reactor while rotating it with a stirrer to 50°C. DIB-diamion is placed here, and through polymerization reaction, linear SBR with a weight average molecular weight (Mw) of about 150,000 g / mol is polymerized. After 10 minutes had elapsed since the reaction temperature reached the highest temperature, 50 g of butadiene was charged, and both ends of the polymer were replaced with butadiene active anions over 5 minutes. Here, DIB-dianion containing modifier diethoxydimethylsilane (diethoxydimethylsilane) was charged at a molar ratio of 2.2 moles, and reacted for 10 minutes. Then, ethanol was added as a reaction terminator to terminate the polymerization, and 0.2 wt% of I-1076 was added as an antioxidant to the polymer to prepare a linear SBR solution.
[0065] ...
Embodiment 2
[0070] 1) Manufacture of linear SBR
[0071] Put 170g of styrene, 630g of 1,3-butadiene, and 4150g of hexane into a 10L autoclave reactor, add 10ml of tetramethylethylenediamine (TMEDA), and raise the temperature of the reactor while rotating it with a stirrer to 50°C. DIB-diamion is placed here, and through polymerization reaction, linear SBR with a weight average molecular weight (Mw) of about 150,000 g / mol is polymerized. After 10 minutes had elapsed since the reaction temperature reached the highest temperature, 50 g of butadiene was charged, and both ends of the polymer were replaced with butadiene active anions over 5 minutes. Here, DIB-diamion containing a modifying agent (3-cyanopropyl)dimethylchlorosilane ((3-Cyanopropyl)dimethylchlorosilane) was charged at a molar ratio of 2.2 moles, and reacted for 10 minutes. Then, ethanol was added as a reaction terminator to terminate the polymerization, and 0.2 wt% of I-1076 was added as an antioxidant to the polymer to prepare ...
Embodiment 3
[0077] 1) Manufacture of linear SBR
[0078] Put 170g of styrene, 630g of 1,3-butadiene, and 4150g of hexane into a 10L autoclave reactor, add 10ml of tetramethylethylenediamine (TMEDA), and raise the temperature of the reactor while rotating it with a stirrer to 50°C. DIB-diamion is placed here, and through polymerization reaction, linear SBR with a weight average molecular weight (Mw) of about 150,000 g / mol is polymerized. After 10 minutes had elapsed since the reaction temperature reached the highest temperature, 50 g of butadiene was charged, and both ends of the polymer were replaced with butadiene active anions over 5 minutes. Here, the modifier 1-(2-chloroethyl)-2,2,5,5-tetramethyl-1-aza-2,5-disilacyclopentyl was added with a molar ratio of 2.2 moles DIB-diamion of alkane (1-(2-chloroethyl)-2,2,5,5-tetramethyl-1-aza-2,5-disilacyclopentane), reacted for 10 minutes. Then, ethanol was added as a reaction terminator to terminate the polymerization, and 0.2 wt% of I-1076 ...
PUM
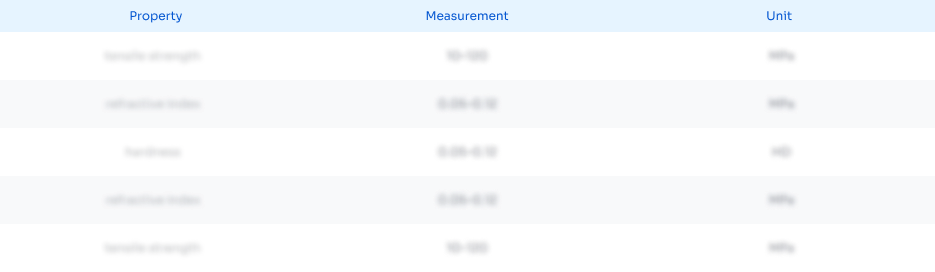
Abstract
Description
Claims
Application Information

- Generate Ideas
- Intellectual Property
- Life Sciences
- Materials
- Tech Scout
- Unparalleled Data Quality
- Higher Quality Content
- 60% Fewer Hallucinations
Browse by: Latest US Patents, China's latest patents, Technical Efficacy Thesaurus, Application Domain, Technology Topic, Popular Technical Reports.
© 2025 PatSnap. All rights reserved.Legal|Privacy policy|Modern Slavery Act Transparency Statement|Sitemap|About US| Contact US: help@patsnap.com