A hydraulic test device for solid rocket motor combustion chamber casing
A hydrostatic test, solid rocket technology, applied in rocket engine devices, machines/engines, jet propulsion devices, etc., can solve the problems of prolonged development cycle, failure of combustion chamber shell, inability to simulate the unloading effect of engine nozzles, etc. The effect of shortened development cycle
- Summary
- Abstract
- Description
- Claims
- Application Information
AI Technical Summary
Problems solved by technology
Method used
Image
Examples
Embodiment Construction
[0014] The present invention will be further described below in combination with specific embodiments.
[0015] A solid rocket motor combustor housing hydraulic test device, such as figure 1 As shown, it includes a load-bearing vertical platform, a thrust frame, a support frame, a water pressure sensor, a combustion chamber shell with a front block cover and a rear block cover, and an unloading mechanism, which is used to simulate the combustion chamber shell The condition that the body is subject to axial pressure enables the hydrostatic test to assess the working condition of the combustion chamber shell bearing axial load while assessing the internal pressure condition of the combustion chamber shell.
[0016] In this embodiment, the unloading mechanism includes an unloading piston and a force transmission and moving mechanism. The unloading piston is dynamically sealed in the axial annular through hole of the front plug cover or the rear plug cover along the axial directio...
PUM
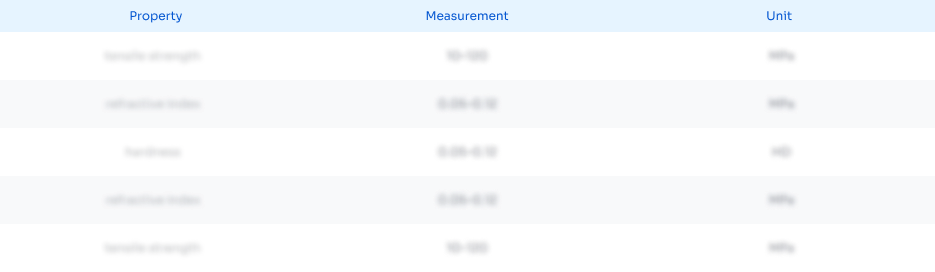
Abstract
Description
Claims
Application Information

- R&D
- Intellectual Property
- Life Sciences
- Materials
- Tech Scout
- Unparalleled Data Quality
- Higher Quality Content
- 60% Fewer Hallucinations
Browse by: Latest US Patents, China's latest patents, Technical Efficacy Thesaurus, Application Domain, Technology Topic, Popular Technical Reports.
© 2025 PatSnap. All rights reserved.Legal|Privacy policy|Modern Slavery Act Transparency Statement|Sitemap|About US| Contact US: help@patsnap.com