Ceramic enhanced ethylene propylene diene monomer material and preparation method
A technology of EPDM rubber and ceramic fiber is applied in the field of solid rocket motor thermal insulation materials, which can solve the problems of inability to form a material carbonized layer, reduce ablation resistance, material peeling, etc. Carbon content, effect of improving ablation resistance
- Summary
- Abstract
- Description
- Claims
- Application Information
AI Technical Summary
Problems solved by technology
Method used
Examples
Embodiment 1
[0020] A ceramic fiber reinforced EPDM material, which is made of the following materials in parts by weight: 100 parts of EPDM rubber, 20 parts of ceramic fiber, 20 parts of white carbon black, and 0.5 parts of stearic acid 1 part, accelerator TMTD 1 part, KH550 1 part, DCP 1 part.
[0021] The specific steps are:
[0022] 1) Knead the EPDM rubber with a kneading machine, first add raw rubber, refine for 1-3 minutes, then add white carbon black and stearic acid, refine for 40-60 minutes, and finally add ceramic fiber and accelerator , KH550, DCP, refining for 20-25 minutes;
[0023] 2) After the mixing is completed, store the rubber material in the internal mixer for 24h-48h, and then carry out vacuum mixing, the refining time is 20-30min, and the temperature is ≤40°C; then, the material is obtained.
[0024] The performance data of the material after vulcanization for 1 hour at 150°C and 2MPa pressure are shown in Table 1.
Embodiment 2
[0026] A ceramic fiber reinforced EPDM material, which is made of the following materials in parts by weight: 100 parts of EPDM rubber, 30 parts of ceramic fiber, 40 parts of white carbon black, and 1 part of stearic acid 1 part, accelerator TMTD 2 parts, KH550 1 part, DCP 2 parts;
[0027] The specific steps are:
[0028] 1) Knead the EPDM rubber with a kneading machine, first add raw rubber, refine for 1-3 minutes, then add white carbon black and stearic acid, refine for 40-60 minutes, and finally add ceramic fiber and accelerator , KH550, DCP, refining for 20-25 minutes;
[0029] 2) After the mixing is completed, store the rubber material in the internal mixer for 24h-48h, and then carry out vacuum mixing, the refining time is 20-30min, and the temperature is ≤40°C; then, the material is obtained.
[0030] The performance data of the material after vulcanization for 1 hour at 150°C and 2MPa pressure are shown in Table 1.
Embodiment 3
[0032] A ceramic fiber reinforced EPDM material, which is made of the following materials in parts by weight: 100 parts of EPDM rubber, 30 parts of aluminum silicate fiber, 40 parts of white carbon black, stearic acid 1 part, accelerator TMTD 2 parts, KH550 1 part, DCP 2 parts;
[0033] The specific steps are:
[0034] 1) Knead the EPDM rubber with a kneading machine, first add raw rubber, refine for 1-3 minutes, then add white carbon black and stearic acid, refine for 40-60 minutes, and finally add ceramic fiber and accelerator , KH550, DCP, refining for 20-25 minutes;
[0035] 2) After the mixing is completed, store the rubber material in the internal mixer for 24h-48h, and then carry out vacuum mixing, the refining time is 20-30min, and the temperature is ≤40°C; then, the material is obtained.
[0036] The performance data of the material after vulcanization for 1 hour at 150°C and 2MPa pressure are shown in Table 1.
PUM
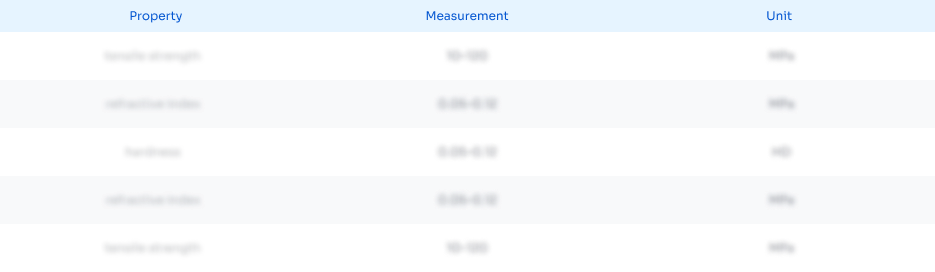
Abstract
Description
Claims
Application Information

- R&D Engineer
- R&D Manager
- IP Professional
- Industry Leading Data Capabilities
- Powerful AI technology
- Patent DNA Extraction
Browse by: Latest US Patents, China's latest patents, Technical Efficacy Thesaurus, Application Domain, Technology Topic, Popular Technical Reports.
© 2024 PatSnap. All rights reserved.Legal|Privacy policy|Modern Slavery Act Transparency Statement|Sitemap|About US| Contact US: help@patsnap.com