Cutting blade
A technology of cutting inserts and inserts, applied in cutting inserts, turning equipment, accessories of tool holders, etc., can solve the problems of reducing the cutting life of cutting inserts, reducing the structural strength of cutting inserts, and the difference of cutting conditions, etc. Effects of vibration, improved cutting accuracy and service life
- Summary
- Abstract
- Description
- Claims
- Application Information
AI Technical Summary
Problems solved by technology
Method used
Image
Examples
Embodiment Construction
[0031] The present invention will be further described in detail below in conjunction with the accompanying drawings and specific embodiments.
[0032] Figure 1 to Figure 5The first embodiment of the cutting insert of the present invention is shown, the cutting insert of this embodiment includes a plate-shaped insert body 1, the insert body 1 is surrounded by an upper surface 2, a lower surface 3 and a side 4 connecting the upper and lower surfaces, The upper surface 2 intersects with the side 4 to form a plurality of cutting units with the same structure. The cutting edge unit includes a minor cutting edge 6, a major cutting edge 7 and a corner cutting edge 8 between the minor cutting edge 6 and the major cutting edge 7. The cutting edge 6 and the main cutting edge 7 are alternately arranged in the circumferential direction of the insert body 1, and the main cutting edge 7 includes a first cutting edge 71, a second cutting edge 72 and a transitional cutting edge connecting t...
PUM
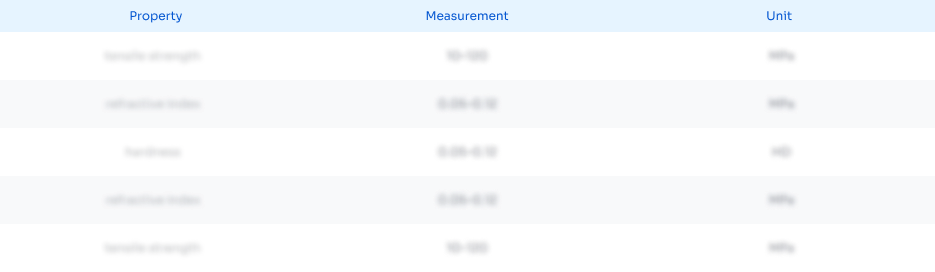
Abstract
Description
Claims
Application Information

- R&D
- Intellectual Property
- Life Sciences
- Materials
- Tech Scout
- Unparalleled Data Quality
- Higher Quality Content
- 60% Fewer Hallucinations
Browse by: Latest US Patents, China's latest patents, Technical Efficacy Thesaurus, Application Domain, Technology Topic, Popular Technical Reports.
© 2025 PatSnap. All rights reserved.Legal|Privacy policy|Modern Slavery Act Transparency Statement|Sitemap|About US| Contact US: help@patsnap.com