Matching method for restraint degrees between actual structure and laboratory sample
A matching method and laboratory technology, which is applied in the field of matching the degree of restraint between the actual structure and the laboratory sample, can solve problems such as unsafe, non-conservative, waste, etc.
- Summary
- Abstract
- Description
- Claims
- Application Information
AI Technical Summary
Problems solved by technology
Method used
Image
Examples
Embodiment Construction
[0029] 1. Establishment of the actual structural finite element model
[0030] Considering the actual working conditions and actual crack size, a finite element model is established for the actual structure, and numerical calculations are performed on the J-integral and strain field at the crack tip (here, ABAQUS / Standard software is used for calculation, but not limited to this software).
[0031] 2. Calculation of the J-Apeeq curve of the actual structure
[0032] Select an appropriate equivalent plastic strain value (PEEQ, the size of PEEQ should only reflect the strain field in the crack tip region without interference from the strain field in other regions. Under this condition, the value of PEEQ can be selected arbitrarily), and Calculate the area Apeeq of the area surrounded by the PEEQ contours under different J integrals to obtain the J-Apeeq curve.
[0033] 3. Establishment of finite element model of laboratory samples
[0034] Select an appropriate laboratory samp...
PUM
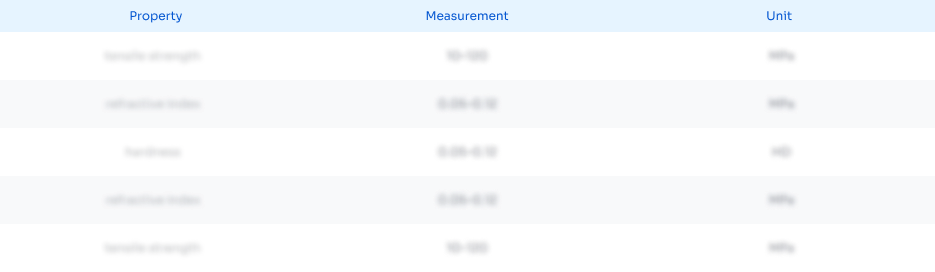
Abstract
Description
Claims
Application Information

- Generate Ideas
- Intellectual Property
- Life Sciences
- Materials
- Tech Scout
- Unparalleled Data Quality
- Higher Quality Content
- 60% Fewer Hallucinations
Browse by: Latest US Patents, China's latest patents, Technical Efficacy Thesaurus, Application Domain, Technology Topic, Popular Technical Reports.
© 2025 PatSnap. All rights reserved.Legal|Privacy policy|Modern Slavery Act Transparency Statement|Sitemap|About US| Contact US: help@patsnap.com