Multi-degree-of-freedom mixed drive artificial muscle
A hybrid drive, artificial muscle technology, applied in the fields of intelligent materials, bionics, and pneumatic muscles, can solve the problems of insufficient muscle strength of fishing lines, troublesome heating, etc., and achieve high power-to-weight ratio, good flexibility, and increased bending freedom. Effect
- Summary
- Abstract
- Description
- Claims
- Application Information
AI Technical Summary
Problems solved by technology
Method used
Image
Examples
Embodiment Construction
[0018] figure 1 It is a schematic diagram of a multi-degree-of-freedom hybrid-driven artificial muscle structure. The specific embodiments of the present invention will be further described below in conjunction with the accompanying drawings.
[0019] A. A layer of PET braided mesh is installed outside the elastic rubber tube, and the two ends are sealed and fastened by inner plug members and outer clamps. In addition, there is a threaded through hole in the middle of the inner plug member for front-end sealing, and the pneumatic joint is connected by thread connection, and the pneumatic joint is connected to the external air pipe to inflate and deflate the rubber pipe. There is a threaded hole with a certain depth on the inner plug member for sealing the rear end, and the rear end fixing frame is fixed by screwing in the screw.
[0020] B. The initial braiding angle of the braided net outside the elastic rubber tube is greater than 54°, which satisfies the requirement tha...
PUM
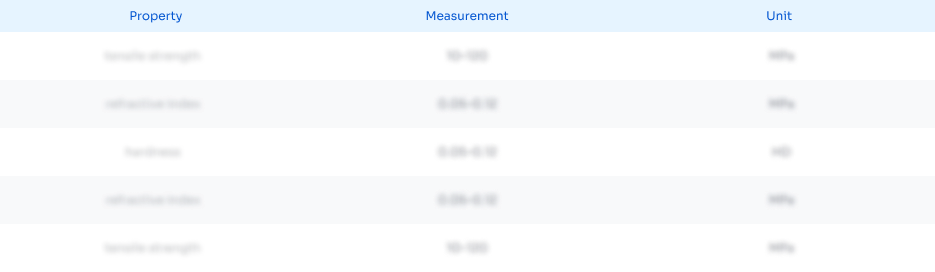
Abstract
Description
Claims
Application Information

- R&D Engineer
- R&D Manager
- IP Professional
- Industry Leading Data Capabilities
- Powerful AI technology
- Patent DNA Extraction
Browse by: Latest US Patents, China's latest patents, Technical Efficacy Thesaurus, Application Domain, Technology Topic, Popular Technical Reports.
© 2024 PatSnap. All rights reserved.Legal|Privacy policy|Modern Slavery Act Transparency Statement|Sitemap|About US| Contact US: help@patsnap.com