Inverter parallel operation optimization control method
A technology of operation optimization and control method, applied in the direction of single grid parallel feeding arrangement, etc., can solve the problems of poor inverter control effect, deterioration of inverter power quality, affecting the normal operation of user equipment or electrical appliances, etc.
- Summary
- Abstract
- Description
- Claims
- Application Information
AI Technical Summary
Problems solved by technology
Method used
Image
Examples
Embodiment Construction
[0052] In order to enable those skilled in the art to better understand the technical solutions in the present invention, the technical solutions in the embodiments of the present invention will be clearly and completely described below in conjunction with the drawings in the embodiments of the present invention. Obviously, the described The embodiments are only some of the embodiments of the present invention, not all of them.
[0053] see figure 2 is the equivalent circuit diagram of parallel inverters, such as figure 2 shown, E and are the RMS value and power angle of the reference voltage; Z and θ are the modulus and impedance angle of the line impedance; R and X are the line resistance and inductance; V b is the effective value of the AC bus voltage.
[0054] From this, it can be obtained that the active power injected by the inverter into the parallel inverter system is:
[0055]
[0056] The reactive power is:
[0057]
[0058] Suppose the introduced virtual...
PUM
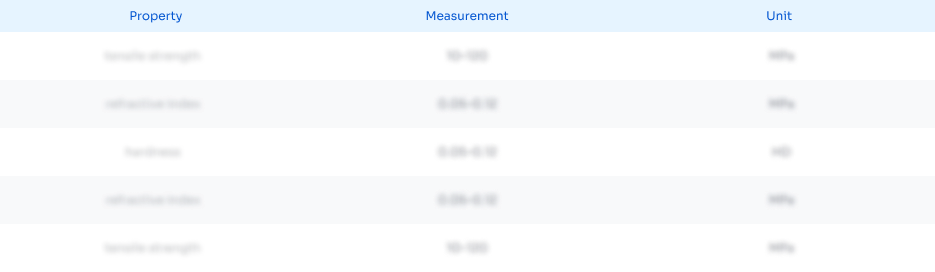
Abstract
Description
Claims
Application Information

- Generate Ideas
- Intellectual Property
- Life Sciences
- Materials
- Tech Scout
- Unparalleled Data Quality
- Higher Quality Content
- 60% Fewer Hallucinations
Browse by: Latest US Patents, China's latest patents, Technical Efficacy Thesaurus, Application Domain, Technology Topic, Popular Technical Reports.
© 2025 PatSnap. All rights reserved.Legal|Privacy policy|Modern Slavery Act Transparency Statement|Sitemap|About US| Contact US: help@patsnap.com