Organic fouling cleaning agent for reverse osmosis membranes
A technology of reverse osmosis membrane and cleaning agent, which is applied in the field of water treatment, can solve the problems of cumbersome procedures and complicated cleaning process, and achieve the effects of good bactericidal performance, less dosage, and improved wettability
- Summary
- Abstract
- Description
- Claims
- Application Information
AI Technical Summary
Problems solved by technology
Method used
Image
Examples
example 1
[0030] Select raw materials according to weight percentage:
[0031] Sodium tetradecylbenzenesulfonate 0.0006%,
[0032] Hexadecyl o-dimethylbenzenesulfonic acid 0.0004%
[0033] Calcium Disodium EDTA Anhydrous 20%
[0034] Sodium hydroxide 0.001%
[0035] Trimetaphosphate Buffer 15%
[0036] 25% aqueous solution of glutaraldehyde 0.001%
[0037] The reverse osmosis system yields 64.997% water.
[0038]First add 64.997% of the reverse osmosis system product water into the reaction kettle, then add 0.0006% sodium tetradecylbenzenesulfonate, 0.0004% hexadecyl o-dimethylbenzenesulfonic acid, 20% anhydrous ethylenediamine Calcium disodium tetraacetate, 0.001% sodium hydroxide, 15% trimetaphosphate buffer solution, 0.001% 25% concentration glutaraldehyde aqueous solution are mixed, and stirring speed is 150 rev / mins, obtains intermediate mixture after dissolving, and water After cooling the intermediate mixture to 25°C, add sodium hydroxide to adjust the pH value of the mixed...
example 2
[0040] Select raw materials according to weight percentage:
[0041] Sodium tetradecylbenzenesulfonate 0.005%
[0042] Calcium Disodium EDTA Anhydrous 45%
[0043] Sodium hydroxide 0.005%
[0044] Trimetaphosphate Buffer 45%
[0045] 25% aqueous solution of glutaraldehyde 0.005%
[0046] The reverse osmosis system yields 9.985% water.
[0047] First add 9.985% of reverse osmosis system product water into the reaction kettle, then add 0.005% sodium tetradecylbenzenesulfonate, 45% anhydrous calcium disodium edetate, 0.005% sodium hydroxide, 45% Trimetaphosphate buffer solution, 0.005% 25% glutaraldehyde aqueous solution are mixed, the stirring speed is 200 rev / min, after dissolving, an intermediate mixture is obtained, after the intermediate mixture is cooled by water to 25°C, sodium hydroxide is added to adjust the mixed solution The pH value is 10.5, just stir until the solution is homogeneous.
example 3
[0049] Sodium tetradecylbenzenesulfonate 0.003%
[0050] Calcium Disodium EDTA Anhydrous 33%
[0051] Sodium hydroxide 0.003%
[0052] Trimetaphosphate buffer 30%
[0053] 25% aqueous solution of glutaraldehyde 0.003%
[0054] The reverse osmosis system yields 36.991% water.
[0055] First add 36.991% of reverse osmosis system product water into the reactor, then add 0.003% sodium tetradecylbenzenesulfonate, 33% anhydrous calcium disodium edetate, 0.003% sodium hydroxide, 30% Trimetaphosphate buffer solution, 0.003% 25% concentration of glutaraldehyde aqueous solution are mixed, the stirring speed is 200 rpm, after dissolving, an intermediate mixture is obtained, after cooling the intermediate mixture with water to 25°C, add sodium hydroxide to adjust the mixed solution The pH value is at 11, just stir until the solution is homogeneous.
PUM
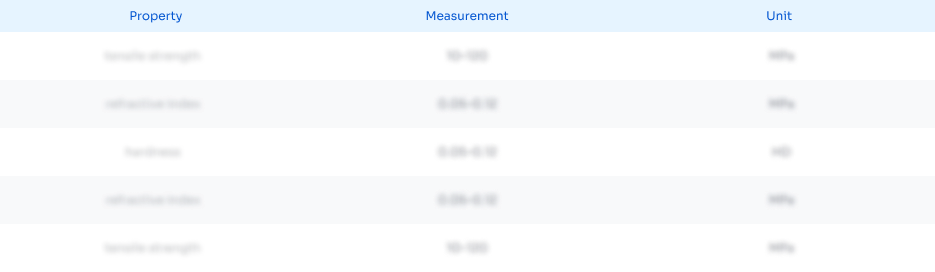
Abstract
Description
Claims
Application Information

- R&D
- Intellectual Property
- Life Sciences
- Materials
- Tech Scout
- Unparalleled Data Quality
- Higher Quality Content
- 60% Fewer Hallucinations
Browse by: Latest US Patents, China's latest patents, Technical Efficacy Thesaurus, Application Domain, Technology Topic, Popular Technical Reports.
© 2025 PatSnap. All rights reserved.Legal|Privacy policy|Modern Slavery Act Transparency Statement|Sitemap|About US| Contact US: help@patsnap.com