Multi-propeller synchronous rotation mechanism for submersible
A technology of synchronous rotation and propulsion, which is used in transmission devices, ship propulsion, and propulsion components using synchronous propulsion components. wide effect
- Summary
- Abstract
- Description
- Claims
- Application Information
AI Technical Summary
Problems solved by technology
Method used
Image
Examples
Embodiment Construction
[0021] The present invention will be described in further detail below in conjunction with the accompanying drawings.
[0022] Such as Figure 1~4 As shown, the present invention includes a mechanism casing 3, a mechanism cover, a mechanism base 16, a right end cover 1, a left end cover 11, a transmission shaft 5, a motor and a reducer assembly 31, a transmission mechanism, a transmission pair, a propeller shaft 34, and a propeller 36. Pipe joint 29 and oil pipe 30, wherein the mechanism cover includes an upper cover 26 and a transparent sealing cover 27, an O-ring sealing ring B4 is installed at the O-ring groove on the upper end surface of the mechanism casing 3, and the sealing cover 27 passes through the O-ring The sealing ring B4 is sealed with the upper end surface of the mechanism casing 3, and the upper cover 26 is located above the sealing cover 27, and is jointly fixed on the mechanism casing 3 by bolts. The sealing cover 27 is transparent, and the material can be a...
PUM
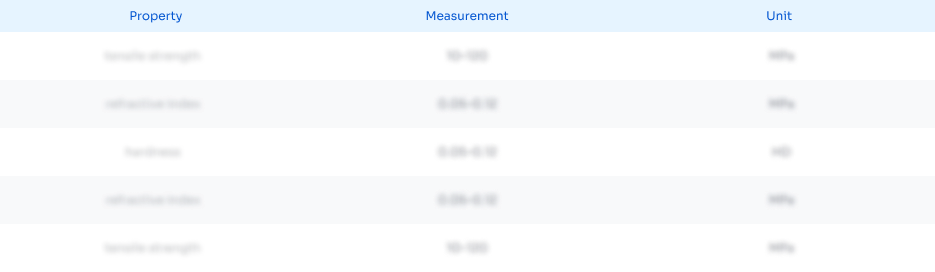
Abstract
Description
Claims
Application Information

- R&D
- Intellectual Property
- Life Sciences
- Materials
- Tech Scout
- Unparalleled Data Quality
- Higher Quality Content
- 60% Fewer Hallucinations
Browse by: Latest US Patents, China's latest patents, Technical Efficacy Thesaurus, Application Domain, Technology Topic, Popular Technical Reports.
© 2025 PatSnap. All rights reserved.Legal|Privacy policy|Modern Slavery Act Transparency Statement|Sitemap|About US| Contact US: help@patsnap.com