ADRC (Active disturbance rejection controller)-PD compensation control system and method for time delay process
A technology of ADRC-PD and compensation control, which is applied in general control system, control/regulation system, program control, etc., can solve the problems of lagging system control difficulty, advanced controller structure complexity, etc., to improve tracking control performance and Effect
- Summary
- Abstract
- Description
- Claims
- Application Information
AI Technical Summary
Problems solved by technology
Method used
Image
Examples
Embodiment 1
[0045] Apply the present invention to a factory to absorb and stabilize industrial production equipment, and refer to the hardware structure diagram of the equipment figure 1 , refer to the process flow of the device Figure 5 . The device mainly controls the temperature of the rectification tower bottom by adjusting the steam flow rate. Due to the hysteresis of the temperature detection, the difficulty of control is increased.
[0046] refer to figure 2 , an ADRC-PD compensation control system and method for a time lag process, including a field instrument connected to the device, a Yokogawa CS3000DCS system, and a DELL 1900 server as a lag compensation server. The lag compensation server includes: an OPC client data communication module and a database interface module. Use the OPC client data acquisition module to collect tower kettle temperature, steam flow and valve opening.
[0047] Through open-loop identification, the open-loop transfer function of the identified o...
Embodiment 2
[0053] Apply the present invention to an industrial methane production device in a factory, and refer to the hardware structure diagram of the device figure 1 , refer to the process flow of the device Figure 7 . The device controls the liquid level of a liquid storage tank. Due to the needs of production, there is a buffer tank in the previous stage of the liquid storage tank. The liquid level of the liquid storage tank is controlled through the feed valve of the buffer tank. There is a large hysteresis in the liquid level control of a multi-capacity device like this.
[0054] Through open-loop identification, the open-loop transfer function of the identified object is:
[0055]
[0056] ADRC-PD compensation control module. It is used for the compensation control of the lagging object, optimizes and calculates the appropriate output value for the feed valve, so that the opening of the valve meets the control requirements of the liquid level.
[0057] After using the pr...
PUM
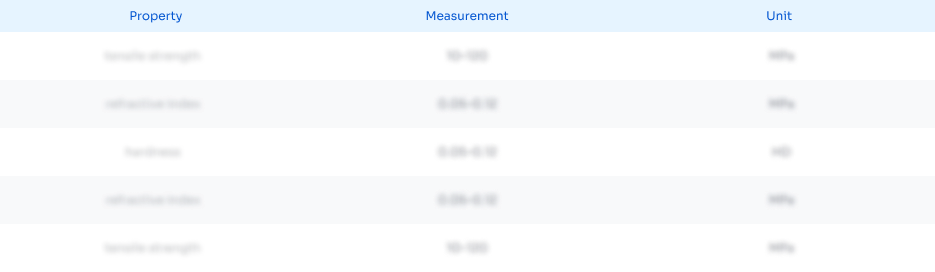
Abstract
Description
Claims
Application Information

- R&D Engineer
- R&D Manager
- IP Professional
- Industry Leading Data Capabilities
- Powerful AI technology
- Patent DNA Extraction
Browse by: Latest US Patents, China's latest patents, Technical Efficacy Thesaurus, Application Domain, Technology Topic, Popular Technical Reports.
© 2024 PatSnap. All rights reserved.Legal|Privacy policy|Modern Slavery Act Transparency Statement|Sitemap|About US| Contact US: help@patsnap.com