Grouting forming method for ceramic blanks
A ceramic body and grouting molding technology, which is applied in the field of ceramic manufacturing, can solve the problems of mold leakage, fast sizing speed, and large slurry supply pressure, and achieve the effect of eliminating slurry leakage and reducing all emptying
- Summary
- Abstract
- Description
- Claims
- Application Information
AI Technical Summary
Problems solved by technology
Method used
Image
Examples
Embodiment Construction
[0024] like Figure 1-3 As shown, a method for grouting a ceramic body, comprising:
[0025] 1. Grouting: Open the grouting pipe 120 and inject mud into the grouting bucket 110 connected to the atmosphere. When the mud in the grouting bucket 110 rises to the first liquid level L1, close the grouting pipe and start grouting. .
[0026] 2. Slurring: Open the slurring pipe 130 and inject the mud into the slurring pipe 140 until the mud in the grouting bucket 110 drops to the second liquid level L2, close the slurring pipe 130 and return to the grouting step.
[0027] 3. Preparation for mud injection molding:
[0028] (1) During the slurrying process, when the liquid level in the horizontal liquid level device 150 on the slurry separating pipe 140 reaches the preset liquid level, close the slurrying pipe, and perform step (2);
[0029] The preset liquid level is flush with the liquid inlet of the mold 190 .
[0030] (2) After the liquid level of the horizontal liquid level gau...
PUM
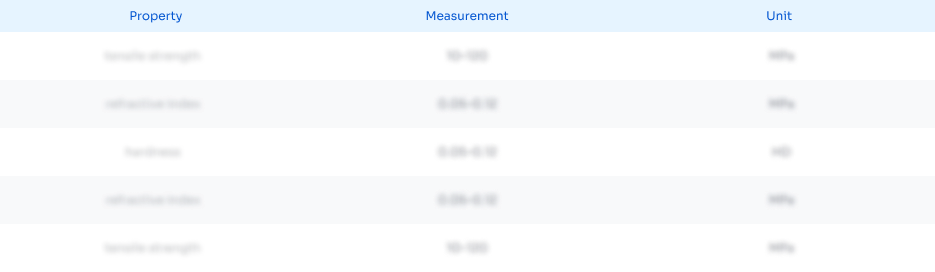
Abstract
Description
Claims
Application Information

- R&D
- Intellectual Property
- Life Sciences
- Materials
- Tech Scout
- Unparalleled Data Quality
- Higher Quality Content
- 60% Fewer Hallucinations
Browse by: Latest US Patents, China's latest patents, Technical Efficacy Thesaurus, Application Domain, Technology Topic, Popular Technical Reports.
© 2025 PatSnap. All rights reserved.Legal|Privacy policy|Modern Slavery Act Transparency Statement|Sitemap|About US| Contact US: help@patsnap.com