Space six degrees of freedom microgravity smart installation platform
A technology of microgravity and degrees of freedom, applied in the direction of instruments and instrument parts, etc., can solve the problems of complex mechanism, laborious handling, insufficient stroke, etc., and achieve the effect of large stroke, high safety and reliability, and strong operability.
Active Publication Date: 2019-06-04
LASER FUSION RES CENT CHINA ACAD OF ENG PHYSICS +1
View PDF3 Cites 0 Cited by
- Summary
- Abstract
- Description
- Claims
- Application Information
AI Technical Summary
Problems solved by technology
[0002] In specific occasions such as research institutes and factories, there are many experimental instruments and products (such as automobiles) that need to be calibrated. These objects to be calibrated include some objects with high quality and high requirements for calibration accuracy. The calibration of some objects to be calibrated has the problem of laborious handling and difficulty in meeting the calibration accuracy requirements. At the same time, unreasonable calibration may have adverse effects on the use of experimental equipment and products.
[0003] In order to adapt to the industrial needs of the new era and solve the above-mentioned problems, a large number of docking installation platforms with six degrees of freedom in space have emerged, and they can all realize docking installations with six degrees of freedom in space, such as the Stewart mechanism proposed by D.Stewart and Eric.Gough. Gough mechanism and other 6‐DOF platforms, but there are many shortcomings, such as complex mechanism, difficult processing and assembly, poor algorithm effect (such as singular point, adjusting pose coupling, etc.), insufficient travel, and difficult trajectory planning Wait
Method used
the structure of the environmentally friendly knitted fabric provided by the present invention; figure 2 Flow chart of the yarn wrapping machine for environmentally friendly knitted fabrics and storage devices; image 3 Is the parameter map of the yarn covering machine
View moreImage
Smart Image Click on the blue labels to locate them in the text.
Smart ImageViewing Examples
Examples
Experimental program
Comparison scheme
Effect test
example
[0044] Level analysis:
[0045]
[0046] Vertical analysis:
[0047]
the structure of the environmentally friendly knitted fabric provided by the present invention; figure 2 Flow chart of the yarn wrapping machine for environmentally friendly knitted fabrics and storage devices; image 3 Is the parameter map of the yarn covering machine
Login to View More PUM
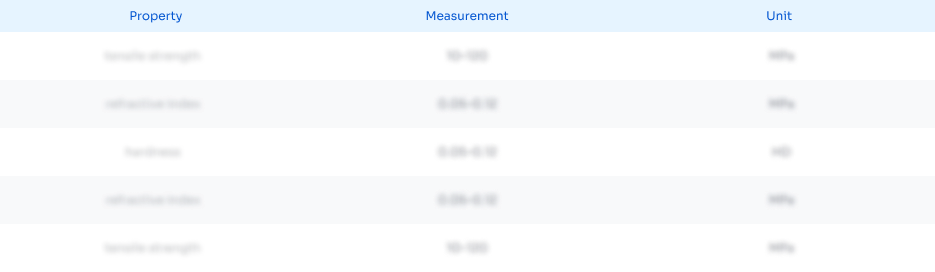
Abstract
The invention discloses a space six-freedom-degree microgravity ingenious assembling and correcting platform which comprises a machine base, a stand column, a rotary table connecting piece, a rotary table and an adjusting mechanism; the lower end portion of the stand column is arranged on the machine base; the upper end portion of the stand column is provided with the rotary table connecting piece; the rotary table is arranged on the rotary table connecting piece; the adjusting mechanism is arranged on the rotary table; and therefore the space six-freedom-degree microgravity ingenious assembling and correcting platform is formed. According to the space six-freedom-degree microgravity ingenious assembling and correcting platform, microgravity assembling and correcting and indifferent equilibrium can be achieved, and the requirement for certain position precision of assembling and correcting is met; and in addition, the space six-freedom-degree microgravity ingenious assembling and correcting platform has the beneficial effects that the stroke is large, operability is high, and safe reliability is high.
Description
technical field [0001] The present invention relates to a space six-degree-of-freedom calibration platform, in particular to a spatial six-degree-of-freedom microgravity smart calibration platform, wherein the space six-degree-of-freedom microgravity smart calibration platform adopts multiple sets of parallelogram linkage mechanisms and micro-gravity The gravity adjustment mechanism can realize the six-degree-of-freedom microgravity docking and calibration of the predetermined target object, and the calibration is flexible and light. Background technique [0002] In specific occasions such as research institutes and factories, there are many experimental instruments and products (such as automobiles) that need to be calibrated. These objects to be calibrated include some objects with high quality and high requirements for calibration accuracy. The calibration of some objects to be calibrated has the problem of laborious handling and difficulty in meeting the calibration accu...
Claims
the structure of the environmentally friendly knitted fabric provided by the present invention; figure 2 Flow chart of the yarn wrapping machine for environmentally friendly knitted fabrics and storage devices; image 3 Is the parameter map of the yarn covering machine
Login to View More Application Information
Patent Timeline

Patent Type & Authority Patents(China)
IPC IPC(8): G12B5/00
CPCG12B5/00
Inventor 范乃吉刘飞张尽力郑万国朱小龙谢志江周海宋宁策袁晓东陈远斌张洪川
Owner LASER FUSION RES CENT CHINA ACAD OF ENG PHYSICS
Features
- R&D
- Intellectual Property
- Life Sciences
- Materials
- Tech Scout
Why Patsnap Eureka
- Unparalleled Data Quality
- Higher Quality Content
- 60% Fewer Hallucinations
Social media
Patsnap Eureka Blog
Learn More Browse by: Latest US Patents, China's latest patents, Technical Efficacy Thesaurus, Application Domain, Technology Topic, Popular Technical Reports.
© 2025 PatSnap. All rights reserved.Legal|Privacy policy|Modern Slavery Act Transparency Statement|Sitemap|About US| Contact US: help@patsnap.com