Design Method of Primary and Secondary Spring Clearance of Non-equal Deviation Frequency One-stage Gradual Stiffness Leaf Spring
A technology of primary and secondary springs and stiffness, applied to spring components, leaf springs, springs, etc. composed of several springs. Achieve the effect of improving design level, speeding up product development, and reducing design and testing costs
- Summary
- Abstract
- Description
- Claims
- Application Information
AI Technical Summary
Problems solved by technology
Method used
Image
Examples
Embodiment
[0042] Embodiment: A non-equal bias frequency one-stage gradient stiffness leaf spring, refer to figure 2 , which includes the main spring 3, the first-stage auxiliary spring 2 and the second-stage auxiliary spring 1, the width of the entire leaf spring b=63mm, half of the span is half the effective length L 1t =525mm, half of the saddle bolt clamping distance L 0 =50mm, elastic modulus E=200GPa. The number of main reeds is n=3, the number of secondary reeds is m=2, and the total number of primary and secondary reeds is N=n+m=5. Among them, the thickness h of each main spring 1 = h 2 = h 3 =8mm, half of the active length of each main spring is L 1t =525mm, L 2t =450mm, L 3t =350mm; half of the clamping length is L 1 =L 1t -L 0 / 2=500mm, L 2 =L 2t -L 0 / 2=425mm, L 3 =L 3t -L 0 / 2=325mm. Thickness h of each secondary spring A1 = h A2 =13mm, half of the working length of each auxiliary spring is L A1t =250mm, L A2t =150mm, half of the clamping length is L A...
PUM
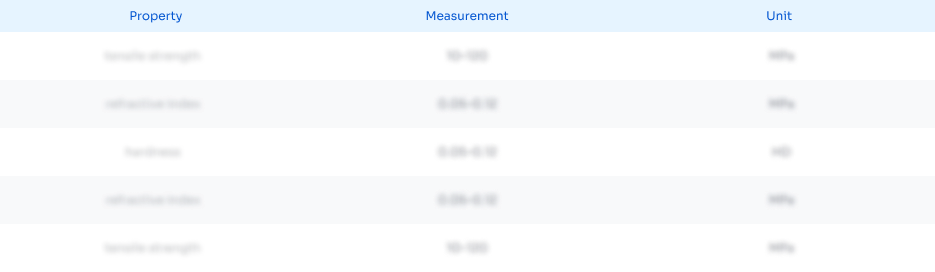
Abstract
Description
Claims
Application Information

- R&D Engineer
- R&D Manager
- IP Professional
- Industry Leading Data Capabilities
- Powerful AI technology
- Patent DNA Extraction
Browse by: Latest US Patents, China's latest patents, Technical Efficacy Thesaurus, Application Domain, Technology Topic, Popular Technical Reports.
© 2024 PatSnap. All rights reserved.Legal|Privacy policy|Modern Slavery Act Transparency Statement|Sitemap|About US| Contact US: help@patsnap.com