Railway vehicle weight gravity center design optimization method and system based on multi-objective optimization
A multi-objective optimization, rail vehicle technology, applied in the rail vehicle weight center of gravity design optimization system, the field of rail vehicle weight center of gravity design optimization, can solve the problems of increased cost, limited within the specified range, increased energy consumption, etc.
- Summary
- Abstract
- Description
- Claims
- Application Information
AI Technical Summary
Problems solved by technology
Method used
Image
Examples
Embodiment Construction
[0049] The following will clearly and completely describe the technical solutions in the embodiments of the present invention with reference to the accompanying drawings in the embodiments of the present invention. Obviously, the described embodiments are only some, not all, embodiments of the present invention. Based on the embodiments of the present invention, all other embodiments obtained by persons of ordinary skill in the art without making creative efforts belong to the protection scope of the present invention.
[0050] Please refer to figure 1 , figure 1 It is a flowchart of a specific embodiment provided by the present invention.
[0051] In a specific embodiment provided by the present invention, the rail vehicle weight center of gravity design optimization method based on multi-objective optimization mainly includes five steps, which are respectively: measuring the current weight and current center of gravity coordinates of each component part of the rail vehicle,...
PUM
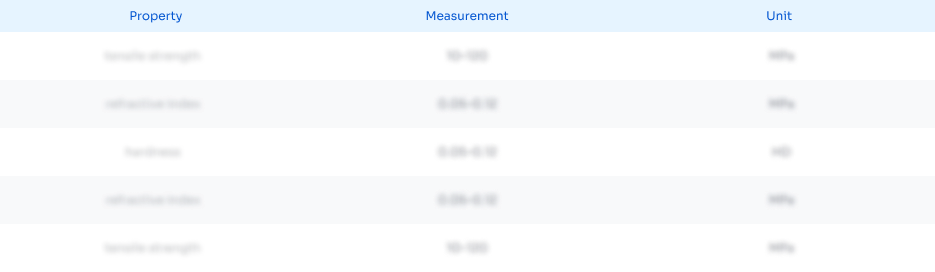
Abstract
Description
Claims
Application Information

- R&D Engineer
- R&D Manager
- IP Professional
- Industry Leading Data Capabilities
- Powerful AI technology
- Patent DNA Extraction
Browse by: Latest US Patents, China's latest patents, Technical Efficacy Thesaurus, Application Domain, Technology Topic, Popular Technical Reports.
© 2024 PatSnap. All rights reserved.Legal|Privacy policy|Modern Slavery Act Transparency Statement|Sitemap|About US| Contact US: help@patsnap.com