Positioning ultrasonic testing device and positioning ultrasonic testing method for plane welding component
A technology of plane welding and ultrasonic testing, which is applied to measuring devices, analyzing solids using sound waves/ultrasonic waves/infrasonic waves, and using sound waves/ultrasonic waves/infrasonic waves for material analysis, etc. It can solve problems such as complex ultrasonic scanning mechanisms and large footprints , to achieve the effect of low processing difficulty, low manufacturing cost and simple structure
- Summary
- Abstract
- Description
- Claims
- Application Information
AI Technical Summary
Problems solved by technology
Method used
Image
Examples
Embodiment Construction
[0038] The details of the present invention and its specific implementation will be further described below in conjunction with the accompanying drawings, taking the detection of honeycomb brazing plate workpieces commonly used in the medical industry as an example.
[0039] see figure 1 and figure 2 As shown, the positioning ultrasonic detection device for plane welded parts of the present invention includes an industrial computer 1 , an ultrasonic probe 7 , an ultrasonic detection module 3 , a series robot arm 4 , an angle sensor and a data acquisition card 6 . The ultrasonic probe 7 is connected with the ultrasonic detection module 3 through the probe connection line. The ultrasonic detection module 3 is composed of an ultrasonic pulse transmitting circuit, an ultrasonic receiving circuit and an A / D analog-to-digital conversion circuit. It is connected with the industrial computer 1 through the PCI bus, and the mechanical arm 4 is connected in series. The mechanical arm s...
PUM
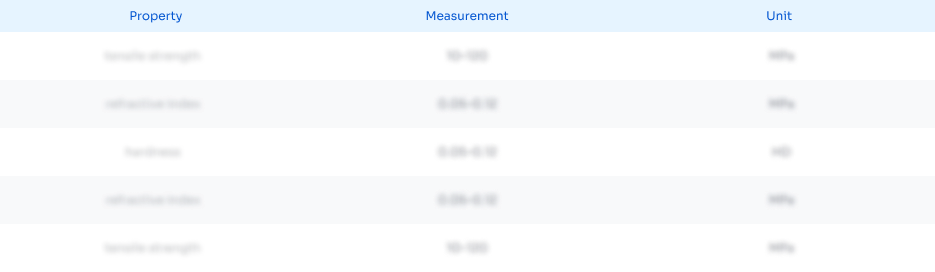
Abstract
Description
Claims
Application Information

- R&D Engineer
- R&D Manager
- IP Professional
- Industry Leading Data Capabilities
- Powerful AI technology
- Patent DNA Extraction
Browse by: Latest US Patents, China's latest patents, Technical Efficacy Thesaurus, Application Domain, Technology Topic, Popular Technical Reports.
© 2024 PatSnap. All rights reserved.Legal|Privacy policy|Modern Slavery Act Transparency Statement|Sitemap|About US| Contact US: help@patsnap.com