Anti-electromagnetic-interference train wheel vibration measurement method based on axle box acceleration
An anti-electromagnetic interference, train wheel technology, applied in vibration testing, railway vehicle testing, machine/structural component testing, etc., can solve the problems of weak anti-electromagnetic interference, high economic cost, complex system composition, etc., and achieve electromagnetic interference Ease of removal and disassembly
- Summary
- Abstract
- Description
- Claims
- Application Information
AI Technical Summary
Problems solved by technology
Method used
Image
Examples
Embodiment Construction
[0017] Below in conjunction with accompanying drawing and embodiment the present invention will be further described:
[0018] as attached figure 1 As shown, wheel set (1), support plate (2), end cap (3), rubber sleeve (4), wireless speed sensor (5), wireless acceleration sensor (6), wireless laser acceleration sensor (7), signal receiver (8), computer (9), rail (10).
[0019] as attached figure 2 As shown, a support plate (2), a rubber sleeve (4), a wireless speed sensor (5), a wireless acceleration sensor (6), and a wireless laser acceleration sensor (7).
[0020] Put the support plate (2) on the end cover (3) of the train wheel set (1) through the rubber sleeve (4), and use fastening bolts to fix the support plate (2) on the end cover (3) plane and horizontally, The strong magnets on the wireless speed sensor (5) and the wireless acceleration sensor (6) are adsorbed on the plane of the supporting plate (2). The signal receiver (8) and the computer (9) are placed in the...
PUM
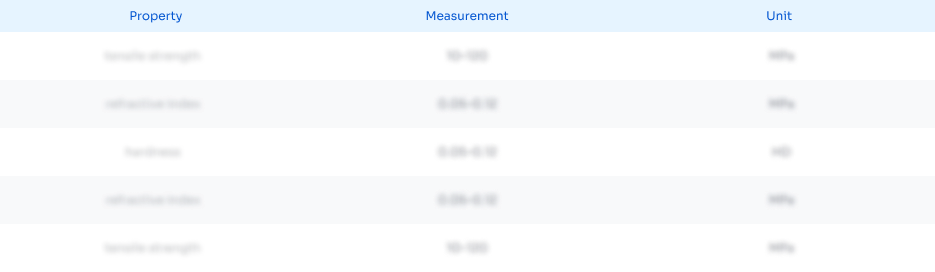
Abstract
Description
Claims
Application Information

- R&D Engineer
- R&D Manager
- IP Professional
- Industry Leading Data Capabilities
- Powerful AI technology
- Patent DNA Extraction
Browse by: Latest US Patents, China's latest patents, Technical Efficacy Thesaurus, Application Domain, Technology Topic, Popular Technical Reports.
© 2024 PatSnap. All rights reserved.Legal|Privacy policy|Modern Slavery Act Transparency Statement|Sitemap|About US| Contact US: help@patsnap.com