Glue, coating fluid and optical composite film
A technology of optical composite film and coating solution, applied in the field of optical film, can solve the problem that optical composite film cannot have high luminance and excellent concealment at the same time
- Summary
- Abstract
- Description
- Claims
- Application Information
AI Technical Summary
Problems solved by technology
Method used
Image
Examples
Embodiment 1
[0084] The invention provides an optical composite film, the composite film includes a brightness enhancing layer and a diffusion layer, the diffusion layer is coated on the back of the brightness enhancement layer, the diffusion layer includes a resin and a resin crystal, and the resin crystal passes through the resin It is bonded to the back of the brightness enhancing layer; the raw material of the diffusion layer is coating liquid.
[0085] The preparation method of above-mentioned optical composite film is as follows:
[0086] 1. Raw material preparation: See Table 1 for the parts by weight of the glue and coating liquid;
[0087] 2. Glue preparation: Mix solid resin slices, methyl ethyl ketone, and toluene into the disperser, seal the dispersing barrel and pour 60°C constant temperature circulating water into the jacket, stirring time 3h, stirring speed 2800r / min; then reduce the stirring Speed up to 800r / min, at the same time reduce the temperature of the constant te...
Embodiment 2
[0093] The preparation process of glue, coating solution and composite film is as in Example 1, and the material composition of glue and coating solution is shown in Table 2.
[0094] Table 2
[0095]
[0096] Wherein, the preparation process of glue is as follows:
[0097] Add the solid resin slices to the organic solvent, heat with 70°C constant temperature circulating water, heat to 70°C, stir at high speed while heating, stir at a high speed of 3000r / min, stir for 4 hours; dissolve the solid resin slices in the organic solvent middle;
[0098] Cool down the obtained resin solution, use constant temperature circulating water at 25°C to cool down, stir at low speed while cooling down, stir at a low speed of 1500r / min, stir for 4 hours to cool down the resin solution to 25°C, and precipitate part of the dissolved resin from the solvent Crystals are formed to obtain the glue.
Embodiment 3
[0100] The preparation process of glue, coating solution and composite film is as in Example 1, and the material composition of glue and coating solution is shown in Table 3.
[0101] table 3
[0102]
[0103] Wherein, the preparation process of glue is as follows:
[0104] Add the solid resin slices to the organic solvent, heat with 60°C constant temperature circulating water, heat to 60°C, stir at high speed while heating, stir at a high speed of 2500r / min, stir for 3 hours; dissolve the solid resin slices in the organic solvent middle;
[0105] Cool down the obtained resin solution, use constant temperature circulating water at 25°C to cool down, stir at a low speed while cooling down, stir at a low speed of 1000r / min, stir for 3.5 hours to cool the resin solution to 25°C, and partially dissolve the resin from the solvent Precipitation forms crystals to obtain the glue.
PUM
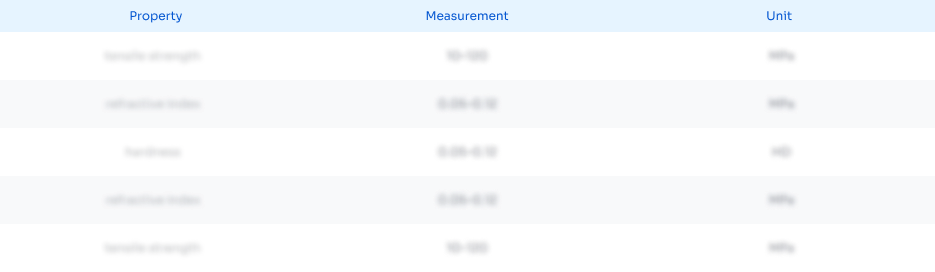
Abstract
Description
Claims
Application Information

- R&D Engineer
- R&D Manager
- IP Professional
- Industry Leading Data Capabilities
- Powerful AI technology
- Patent DNA Extraction
Browse by: Latest US Patents, China's latest patents, Technical Efficacy Thesaurus, Application Domain, Technology Topic, Popular Technical Reports.
© 2024 PatSnap. All rights reserved.Legal|Privacy policy|Modern Slavery Act Transparency Statement|Sitemap|About US| Contact US: help@patsnap.com