A welding process for aluminum alloy
A welding process and aluminum alloy technology, which is applied in welding equipment, welding medium, welding equipment, etc., can solve problems such as incomplete penetration, decreased strength, and affecting the quality of aluminum alloy welding products, and achieve the effect of reducing pores and virtual welding
- Summary
- Abstract
- Description
- Claims
- Application Information
AI Technical Summary
Problems solved by technology
Method used
Image
Examples
Embodiment 1
[0026] A welding process for aluminum alloys, comprising the steps of:
[0027] (1) Put the welding area on the surface of the aluminum alloy plate to be welded into a cleaning solution, the cleaning solution is mainly made of the following raw materials in parts by weight: 10 parts of acetone, 5 parts of ethylene glycol butyl ester, 5 parts of boric acid, phosphoric acid 8 parts of trisodium and 50 parts of deionized water; ultrasonic cleaning was carried out at a temperature of 25°C, the ultrasonic cleaning time was 2min, and the frequency was 20kHz, and then dried in a vacuum drying oven, the drying temperature was controlled at 90°C, and the time 20min;
[0028] (2) Heating the welding area of the aluminum alloy plate to be welded to 150°C for preheating;
[0029] (3) Heating the welding area of the aluminum alloy plate to be welded to 750°C, spraying a degasser on the welding area of the aluminum alloy plate, the degasser is mainly made of the following raw materia...
Embodiment 2
[0034] A welding process for aluminum alloys, comprising the steps of:
[0035] (1) Put the welding area on the surface of the aluminum alloy plate to be welded into a cleaning solution, the cleaning solution is mainly made of the following raw materials in parts by weight: 15 parts of acetone, 12 parts of ethylene glycol butyl ester, 10 parts of boric acid, phosphoric acid 15 parts of trisodium and 80 parts of deionized water; Ultrasonic cleaning was carried out at a temperature of 55°C, the ultrasonic cleaning time was 6min, and the frequency was 26kHz, and then dried in a vacuum drying oven, the drying temperature was controlled at 150°C, and the time 35min;
[0036] (2) Heating the welding area of the aluminum alloy plate to be welded to 200°C for preheating;
[0037](3) Heating the welding area of the aluminum alloy plate to be welded to 830°C, spraying a degasser on the welding area of the aluminum alloy plate, the degasser is mainly made of the following raw mate...
Embodiment 3
[0042] A welding process for aluminum alloys, comprising the steps of:
[0043] (1) Put the welding area on the surface of the aluminum alloy plate to be welded into a cleaning solution, the cleaning solution is mainly made of the following raw materials in parts by weight: 10 parts of acetone, 5 parts of ethylene glycol butyl ester, 5 parts of boric acid, phosphoric acid 8 parts of trisodium and 50 parts of deionized water; ultrasonic cleaning was carried out at a temperature of 25°C, the ultrasonic cleaning time was 2min, and the frequency was 20kHz, and then dried in a vacuum drying oven, the drying temperature was controlled at 90°C, and the time 20min;
[0044] (2) Heating the welding area of the aluminum alloy plate to be welded to 150°C for preheating;
[0045] (3) Heating the welding area of the aluminum alloy plate to be welded to 750°C, spraying a degasser on the welding area of the aluminum alloy plate, the degasser is mainly made of the following raw materia...
PUM
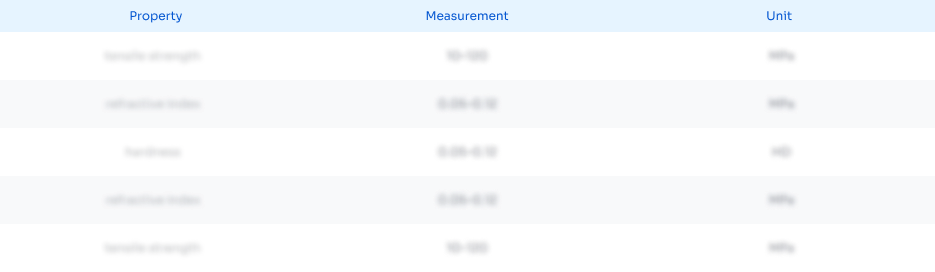
Abstract
Description
Claims
Application Information

- R&D Engineer
- R&D Manager
- IP Professional
- Industry Leading Data Capabilities
- Powerful AI technology
- Patent DNA Extraction
Browse by: Latest US Patents, China's latest patents, Technical Efficacy Thesaurus, Application Domain, Technology Topic, Popular Technical Reports.
© 2024 PatSnap. All rights reserved.Legal|Privacy policy|Modern Slavery Act Transparency Statement|Sitemap|About US| Contact US: help@patsnap.com