Limited space constraint based dynamic co-simulation method of injection manipulator
A limited space, co-simulation technology, applied in the direction of constraint-based CAD, design optimization/simulation, special data processing applications, etc., to achieve the effects of motion time optimization, rapid convergence, and stable calculation
- Summary
- Abstract
- Description
- Claims
- Application Information
AI Technical Summary
Problems solved by technology
Method used
Image
Examples
Embodiment 1
[0058] Embodiment 1: A co-simulation method for dynamics of an injection molding manipulator with limited space constraints, the method includes the following steps:
[0059] (1) Modeling the multi-degree-of-freedom injection molding manipulator: firstly, simplify the model of the manipulator, use UG 3D software to build a 3D model of the manipulator, drive its size change through expressions, store the model size in the database, and modify and add it arbitrarily Data or design variables, the model is automatically updated synchronously, and the expression drives the modeling of the long arm of the manipulator. The schematic diagram of the movement trajectory of the manipulator in the limited space under the limited space constraints, such as figure 1 As shown in the figure, A, B: injection molding machine; C: mechanical arm; D: conveyor belt;
[0060] Table 1 Expressions driving mechanical long arm modeling
[0061] parameter name Calculation formula Calculate...
PUM
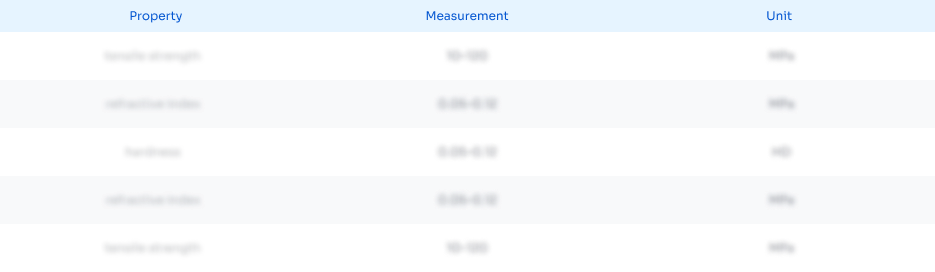
Abstract
Description
Claims
Application Information

- Generate Ideas
- Intellectual Property
- Life Sciences
- Materials
- Tech Scout
- Unparalleled Data Quality
- Higher Quality Content
- 60% Fewer Hallucinations
Browse by: Latest US Patents, China's latest patents, Technical Efficacy Thesaurus, Application Domain, Technology Topic, Popular Technical Reports.
© 2025 PatSnap. All rights reserved.Legal|Privacy policy|Modern Slavery Act Transparency Statement|Sitemap|About US| Contact US: help@patsnap.com