AutoCAD (Autodesk Computer Aided Design) based plate nesting method
A panel and software technology, applied in the field of panel layout based on AutoCAD, can solve the problems of high cost, waste, cutting waste, etc., and achieve the effect of reducing scrap, waste, and operation difficulty
- Summary
- Abstract
- Description
- Claims
- Application Information
AI Technical Summary
Problems solved by technology
Method used
Image
Examples
Embodiment 1
[0034] In this embodiment, the 45# steel plate of 5000 × 3000 × 5 (mm) is used as raw material, and the area is respectively 14500mm 2 、11300mm 2 、8400mm 2 、7200mm 2 、5600mm 2 、4800mm 2 The plate part to be processed is the object of description and the method of the present invention is described in detail:
[0035] like figure 1 As shown, a method for panel layout based on AutoCAD includes the following steps:
[0036] Step 1, divide the area to 14500mm according to the size of the area 2 The part number figure one 1, the area is 11300mm 2 The part number is figure two 2, ..., and so on, the area is 4800mm 2 The part number is figure six 6;
[0037] Step 2, draw the figure 1 of the plate part to be processed through the AutoCAD software, specifically take the zero coordinate as the origin, and draw the longest side A of the figure 1 1 one endpoint of the edge a 1 at the origin, place A 1 Place the side on the X or Y axis, and draw a graph 1;
[0038] Step 3, dr...
Embodiment 2
[0047] A method for panel layout based on AutoCAD, which is basically the same as Embodiment 1, the difference is that, considering the loss of corners of parts by cutting, the drawing size of this embodiment leaves a margin of 5-10mm when drawing graphics , to offset the loss generated by the cutting process.
Embodiment 3
[0049] In Example 1, the graphics are first arranged in the order of the graphics area from large to small, and then the layout is carried out according to the method of step 2-step 6, but because the graphics are sorted and drawn according to the order of different sizes, the results of the layout are not the same, so this paper The embodiment increases the step of optimization of material discharge, specifically as follows:
[0050] First calculate the remaining amount of materials β when each graph is drawn in different orders, wherein the remaining amount of materials β is the minimum value after the area of the graphics in Example 1 is arranged from large to small:
[0051]
[0052] where S i Be the area of each figure, n is the number of figures, and the present embodiment is 6, and i is the sequence number of each figure; Therefore
[0053] The parallel line of the Y axis passes through the point with the largest absolute value of x among the coordinate valu...
PUM
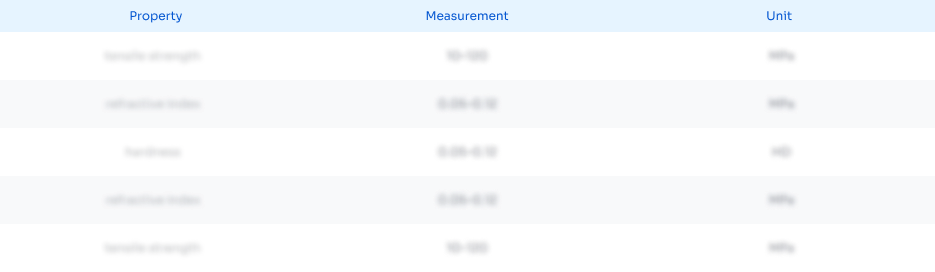
Abstract
Description
Claims
Application Information

- R&D
- Intellectual Property
- Life Sciences
- Materials
- Tech Scout
- Unparalleled Data Quality
- Higher Quality Content
- 60% Fewer Hallucinations
Browse by: Latest US Patents, China's latest patents, Technical Efficacy Thesaurus, Application Domain, Technology Topic, Popular Technical Reports.
© 2025 PatSnap. All rights reserved.Legal|Privacy policy|Modern Slavery Act Transparency Statement|Sitemap|About US| Contact US: help@patsnap.com