Winding mechanism without torsion
A wire winding and reel technology, applied in the field of non-twist wire winding mechanism, can solve the problem of easy torsion of the cable, and achieve the effect of easy handling, small number of parts and compact structure
- Summary
- Abstract
- Description
- Claims
- Application Information
AI Technical Summary
Problems solved by technology
Method used
Image
Examples
Embodiment Construction
[0019] The present invention will be described in further detail below with reference to the drawings.
[0020] Such as figure 1 As shown, the present invention includes a driving reel 1, an intermediate reel 2, a fixed reel 3, a rotating shaft 4, a bearing seat 5, a support frame 6 and a caster 7, wherein the driving reel 1, the intermediate reel 2 and the fixed reel 3 The outer diameters are equal, and the axial lengths of the driving drum 1 and the fixed drum 3 are the same. They are mainly used for winding cables. The specific length depends on the cable length and diameter; the intermediate drum 2 is mainly used to guide the cables. The length depends on the cable bending radius. The rotating shaft 4 passes through the driving drum 1, the intermediate drum 2 and the fixed drum 3 respectively, and is coaxially connected with the driving drum 1, the intermediate drum 2 and the fixed drum 3. The supporting frame 6 is a rectangular parallelepiped-shaped frame, the two ends of t...
PUM
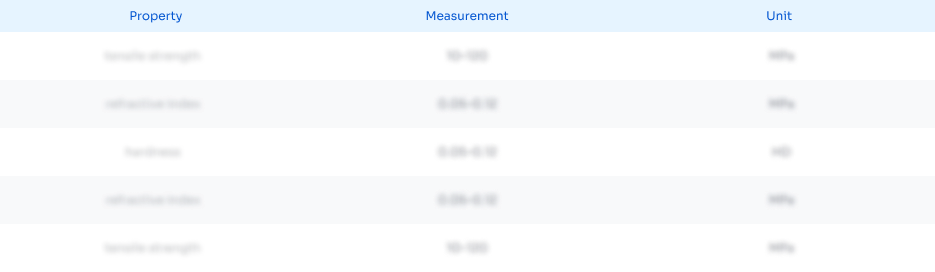
Abstract
Description
Claims
Application Information

- R&D
- Intellectual Property
- Life Sciences
- Materials
- Tech Scout
- Unparalleled Data Quality
- Higher Quality Content
- 60% Fewer Hallucinations
Browse by: Latest US Patents, China's latest patents, Technical Efficacy Thesaurus, Application Domain, Technology Topic, Popular Technical Reports.
© 2025 PatSnap. All rights reserved.Legal|Privacy policy|Modern Slavery Act Transparency Statement|Sitemap|About US| Contact US: help@patsnap.com