Thermal forming method for rigid foam core material
A rigid foam and thermoforming technology, which is applied in the field of composite material manufacturing, can solve the problems of wasting materials and achieve the effect of solving waste materials
- Summary
- Abstract
- Description
- Claims
- Application Information
AI Technical Summary
Problems solved by technology
Method used
Image
Examples
Embodiment Construction
[0020] The present invention is described in detail below in conjunction with accompanying drawing:
[0021] A method for thermoforming a rigid foam core material, the steps of the method are as follows:
[0022] 1) Place the PMI foam board on the molding die 5 according to the theoretical position;
[0023] 2) Stick Airpad rubber 1 on both ends of the PMI foam board with pressure-sensitive tape to prevent the vacuum bag 2 from being sucked between the PMI foam board 4 and the mold, resulting in poor molding of the PMI foam;
[0024] 3) Lay a layer of air felt 3 on the foam board, seal the PMI foam with a vacuum bag 2 and a putty strip, and place a thermocouple on the edge of the air felt;
[0025] 4) Install the quick release nozzle on the mold;
[0026] 5) Connect the quick release nozzle on the mold to the vacuum equipment of the curing furnace through the vacuum pipeline, and then connect the thermocouple to the curing furnace;
[0027] 6) Raise the temperature to 190°C...
PUM
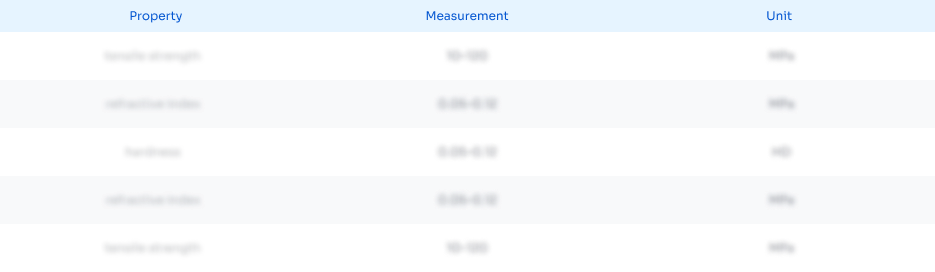
Abstract
Description
Claims
Application Information

- R&D Engineer
- R&D Manager
- IP Professional
- Industry Leading Data Capabilities
- Powerful AI technology
- Patent DNA Extraction
Browse by: Latest US Patents, China's latest patents, Technical Efficacy Thesaurus, Application Domain, Technology Topic, Popular Technical Reports.
© 2024 PatSnap. All rights reserved.Legal|Privacy policy|Modern Slavery Act Transparency Statement|Sitemap|About US| Contact US: help@patsnap.com