Steam type high fineness and no-weldlines injection moulding process for complex precise plastic product
An injection molding process and technology for plastic products, which is applied in the field of steam-type high-gloss seamless injection molding process, can solve the problems of product production efficiency decline, fast speed at thin wall parts, and low molding pass rate, so as to reduce environmental pollution and improve Effect of appearance quality and process cost reduction
- Summary
- Abstract
- Description
- Claims
- Application Information
AI Technical Summary
Problems solved by technology
Method used
Image
Examples
specific Embodiment 1
[0023] Such as figure 1 As shown, it is a steam-type high-gloss seamless injection molding process for complex precision plastic products described in this embodiment, which specifically includes the following steps:
[0024] Step (1), material selection: select PMMA or PC / ABS or high-gloss ABS material as the injection material;
[0025] Step (2), heat recovery treatment: place the injection molding material in a vacuum condensation box to condense at 5°C for 1.0 hour, then place the injection molding material in a vacuum drying oven at 85°C for 2.5 hours to make the humidity less than 0.02%, and then Adopt automatic feeding system for continuous feeding;
[0026] Step (4), mold preheating: correctly install the injection mold on the injection molding machine, and preheat the injection mold by passing high-temperature dry hot air before the mold is closed, and the preheating temperature is set to 75°C;
[0027] Step (5), mold closing (rapid heating): When closing the mold, ...
specific Embodiment 2
[0037] Such as figure 1 As shown, it is a steam-type high-gloss seamless injection molding process for complex precision plastic products described in this embodiment, which specifically includes the following steps:
[0038] Step (1), material selection: select PMMA or PC / ABS or high-gloss ABS material as the injection material;
[0039]Step (2), heat recovery treatment: place the injection molding material in a vacuum condensation box to condense at 7.5°C for 1.5 hours, then place the injection molding material in a vacuum drying oven at 90°C for 3.0 hours to make the humidity less than 0.02%, and then Adopt automatic feeding system for continuous feeding;
[0040] Step (4), mold preheating: correctly install the injection mold on the injection molding machine, and preheat the injection mold by passing high-temperature dry hot air before the mold is closed, and the preheating temperature is set to 85°C;
[0041] Step (5), mold closing (rapid heating): When closing the mold...
specific Embodiment 3
[0051] like figure 1 As shown, it is a steam-type high-gloss seamless injection molding process for complex precision plastic products described in this embodiment, which specifically includes the following steps:
[0052] Step (1), material selection: select PMMA or PC / ABS or high-gloss ABS material as the injection material;
[0053] Step (2), heat recovery treatment: place the injection molding material in a vacuum condensation box to condense at 10°C for 2.0 hours, then place the injection molding material in a vacuum drying oven at 95°C for 3.5 hours to make the humidity less than 0.02%, and then take Automatic feeding system for continuous feeding;
[0054] Step (4), mold preheating: correctly install the injection mold on the injection molding machine, and preheat the injection mold by passing high-temperature dry hot air before the mold is closed, and the preheating temperature is set to 95°C;
[0055] Step (5), mold closing (rapid heating): when closing the mold, a ...
PUM
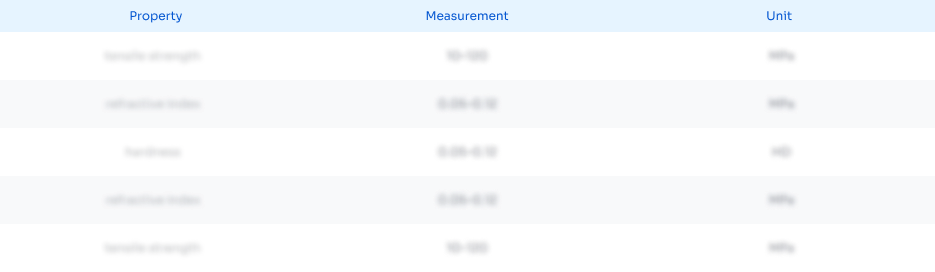
Abstract
Description
Claims
Application Information

- Generate Ideas
- Intellectual Property
- Life Sciences
- Materials
- Tech Scout
- Unparalleled Data Quality
- Higher Quality Content
- 60% Fewer Hallucinations
Browse by: Latest US Patents, China's latest patents, Technical Efficacy Thesaurus, Application Domain, Technology Topic, Popular Technical Reports.
© 2025 PatSnap. All rights reserved.Legal|Privacy policy|Modern Slavery Act Transparency Statement|Sitemap|About US| Contact US: help@patsnap.com