Improved target furnace equipment and target bonding method
An improved target material technology, applied in welding equipment, metal processing equipment, metal processing, etc., can solve the problems of low sintering pass rate, high risk of later use, low melting point of indium, etc., and achieve simple manual operation procedures and bonding The effect of improving efficiency
- Summary
- Abstract
- Description
- Claims
- Application Information
AI Technical Summary
Problems solved by technology
Method used
Image
Examples
Embodiment 1
[0028] Such as figure 1 In the shown improved target furnace equipment, a furnace door 2 is set on one side of the furnace body 1, a heating base 3 is set inside the furnace body 1, and a heating device and a temperature detector for temperature control are installed inside the heating base 3 , the heating base 3 is bolted to the target substrate 4 for placing the target 5, and a stainless steel pressure plate 6 is arranged directly above the target substrate 4, and the length and width of the pressure plate 6 are not smaller than the target The length and width of the substrate 4, the upper end of the pressure plate 6 is connected to the manual pressure valve 8 outside the furnace body 1, there are two manual pressure valves 8, and the lower end of the manual pressure valve 8 is connected to the bottom of the pressure plate 6 respectively. At both ends, the interior of the furnace body 1 communicates with the external vacuum pump 7 .
Embodiment 2
[0030] A method for target bonding using the improved target furnace equipment described in Example 1: specifically comprising the following steps:
[0031] 1) First install a mold on the target substrate 4 and fix it;
[0032] 2) Place the indium balls in the mold and spread them evenly;
[0033] 3) The target material 5 is placed on the indium ball, and it is closely attached to the mold and fixed to ensure that no displacement occurs during the heating and pressing process;
[0034] 4) Use the manual pressure valve 8 to move down the pressure plate 6 to ensure that the pressure plate 6 and the target 5 are tightly locked, and close the furnace door 2;
[0035] 5) Turn on the vacuum pump 7 to pump the vacuum chamber of the equipment to 10Pa;
[0036] 6) Set the pressure value so that the pressure between the target substrate 4 and the target 5 is always maintained at about 2MPa; turn on the heating function to raise the temperature of the heating base 3 to 156°C;
[0037]...
Embodiment 3
[0040] The structure of each part of an improved target furnace equipment described in this embodiment is the same as that in Embodiment 1, and the different technical parameters are: the material of the pressure plate 6 is polytetrafluoroethylene.
PUM
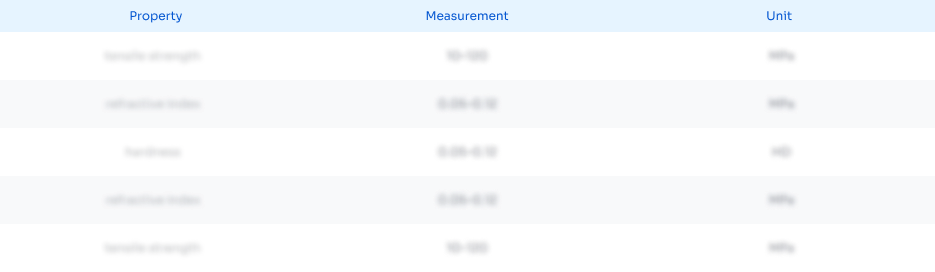
Abstract
Description
Claims
Application Information

- Generate Ideas
- Intellectual Property
- Life Sciences
- Materials
- Tech Scout
- Unparalleled Data Quality
- Higher Quality Content
- 60% Fewer Hallucinations
Browse by: Latest US Patents, China's latest patents, Technical Efficacy Thesaurus, Application Domain, Technology Topic, Popular Technical Reports.
© 2025 PatSnap. All rights reserved.Legal|Privacy policy|Modern Slavery Act Transparency Statement|Sitemap|About US| Contact US: help@patsnap.com