High-speed oil-gas lubrication electric spindle achieving precise oil supplying
A high-speed motorized spindle, oil and gas lubrication technology, applied in the direction of large fixed members, metal processing machinery parts, maintenance and safety accessories, etc., can solve the problems of low precision, increased bearing temperature rise, large bearing oil supply, etc. Precise control, improve lubricating performance, increase the effect of limiting speed
- Summary
- Abstract
- Description
- Claims
- Application Information
AI Technical Summary
Problems solved by technology
Method used
Image
Examples
Embodiment Construction
[0027] The following will clearly and completely describe the technical solutions in the embodiments of the present invention with reference to the accompanying drawings in the embodiments of the present invention. Obviously, the described embodiments are only some, not all, embodiments of the present invention. Based on the embodiments of the present invention, all other embodiments obtained by persons of ordinary skill in the art without making creative efforts fall within the protection scope of the present invention.
[0028] combine figure 1 , 2 , 3, 4 and specific implementation examples, the present invention is further described:
[0029] The electric spindle of the present invention includes a mandrel 1, a front bearing 2, a front bearing chamber 4, a casing 5, a stator 6, a water jacket 7, a rotor 8, a rear bearing chamber 9, a rear bearing 10 and the like. The front and rear bearing chambers are connected through a housing 5, a stator 6 is fixed inside the housing...
PUM
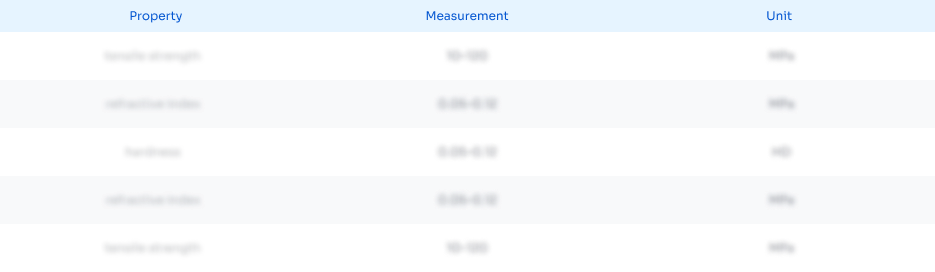
Abstract
Description
Claims
Application Information

- R&D
- Intellectual Property
- Life Sciences
- Materials
- Tech Scout
- Unparalleled Data Quality
- Higher Quality Content
- 60% Fewer Hallucinations
Browse by: Latest US Patents, China's latest patents, Technical Efficacy Thesaurus, Application Domain, Technology Topic, Popular Technical Reports.
© 2025 PatSnap. All rights reserved.Legal|Privacy policy|Modern Slavery Act Transparency Statement|Sitemap|About US| Contact US: help@patsnap.com