Method for accurately positioning casting blank production process parameters to casting blank slices
A production process and accurate positioning technology, applied in the field of intelligent control of continuous casting production process, can solve problems such as slab slicing, parameter positioning deviation, etc., and achieve the effect of ensuring accuracy, high reliability, and accurate and reliable information
- Summary
- Abstract
- Description
- Claims
- Application Information
AI Technical Summary
Problems solved by technology
Method used
Image
Examples
Embodiment
[0117] This embodiment is the actual situation that a steel factory uses this method in the actual production process, and the initial information is:
[0118] Casting machine: 1# casting machine; number of streams: 6 streams; pouring times: 6C3055; furnace number: 1632001;
[0119] (1) According to the weight of molten steel in the ladle, the number of casting streams, the planned fixed length of the slab, the fixed width of the slab, the fixed thickness of the slab and the planned length of the slab, determine the number of slabs planned to be produced per flow and the number of slices per slab .
[0120] Number of slabs generated per flow plan:
[0121] The formula for the number of slabs produced per flow plan is as follows:
[0122]
[0123] Calculated according to formula (a)
[0124] The number of slab slices generated by each slab plan:
[0125] After determining the number of slabs planned to be produced for each stream, use the following formula to determine...
PUM
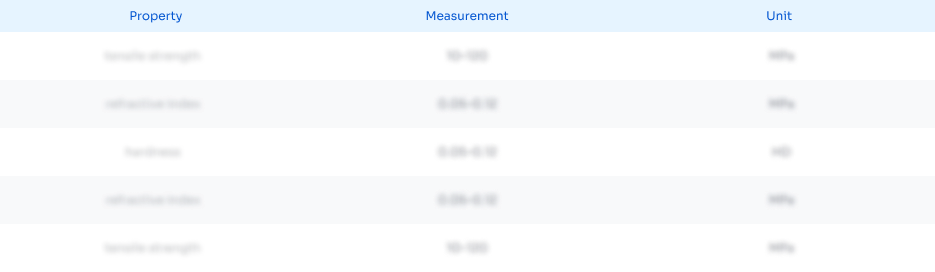
Abstract
Description
Claims
Application Information

- R&D Engineer
- R&D Manager
- IP Professional
- Industry Leading Data Capabilities
- Powerful AI technology
- Patent DNA Extraction
Browse by: Latest US Patents, China's latest patents, Technical Efficacy Thesaurus, Application Domain, Technology Topic, Popular Technical Reports.
© 2024 PatSnap. All rights reserved.Legal|Privacy policy|Modern Slavery Act Transparency Statement|Sitemap|About US| Contact US: help@patsnap.com