Production technique for suspension springs
A production process and suspension spring technology, applied in the production technology field of suspension springs, can solve the problems of poor fatigue strength of suspension springs, consumption of suspension springs, quenching deformation of steel wires, etc., to improve stress relaxation resistance, shorten winding time, The effect of reducing quenching deformation
- Summary
- Abstract
- Description
- Claims
- Application Information
AI Technical Summary
Problems solved by technology
Method used
Examples
Embodiment 1
[0029] A production process of a suspension spring, comprising the following production steps:
[0030] The first step is winding. The spring is wound around the main body of the suspension spring according to the prefabricated height, outer diameter and number of turns. At the same time, the shackles at both ends and the main body of the suspension spring are drawn into shape at one time to obtain the initial product suspension spring.
[0031] The second step is tempering to relieve stress. Put the primary product suspension spring into the tempering furnace for tempering and stress relief, which specifically includes two tempering and stress relief steps:
[0032] For the first tempering to relieve stress, put the primary product suspension spring into the tempering furnace, the temperature in the tempering furnace is 400°C, and the tempering time is 60 minutes;
[0033] For the second tempering to relieve stress, put the first finished product suspension spring into the te...
Embodiment 2
[0048] A production process of a suspension spring, comprising the following production steps:
[0049] The first step is winding. The spring is wound around the main body of the suspension spring according to the prefabricated height, outer diameter and number of turns. At the same time, the shackles at both ends and the main body of the suspension spring are drawn into shape at one time to obtain the initial product suspension spring.
[0050] The second step is tempering to relieve stress. Put the primary product suspension spring into the tempering furnace for tempering and stress relief, which specifically includes two tempering and stress relief steps:
[0051] For the first tempering to relieve stress, put the initial finished suspension spring into the tempering furnace, the temperature in the tempering furnace is 500°C, and the tempering time is 45 minutes;
[0052] For the second tempering to relieve stress, put the first finished product suspension spring into the t...
Embodiment 3
[0067] A production process of a suspension spring, comprising the following production steps:
[0068] The first step is winding. The spring is wound around the main body of the suspension spring according to the prefabricated height, outer diameter and number of turns. At the same time, the shackles at both ends and the main body of the suspension spring are drawn into shape at one time to obtain the initial product suspension spring.
[0069] The second step is tempering to relieve stress. Put the primary product suspension spring into the tempering furnace for tempering and stress relief, which specifically includes two tempering and stress relief steps:
[0070] For the first tempering to relieve stress, put the initial finished suspension spring into the tempering furnace, the temperature in the tempering furnace is 650°C, and the tempering time is 30 minutes;
[0071] For the second tempering to relieve stress, put the first finished product suspension spring into the t...
PUM
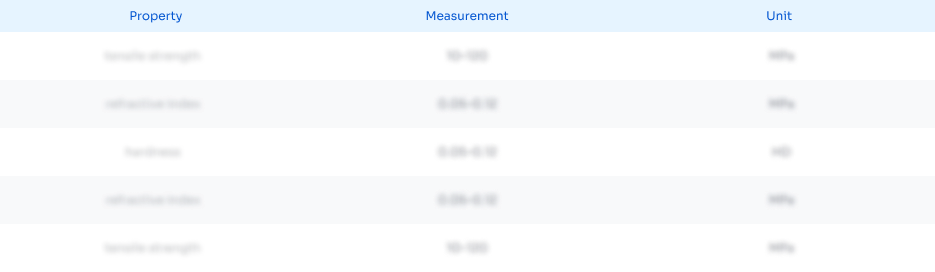
Abstract
Description
Claims
Application Information

- R&D Engineer
- R&D Manager
- IP Professional
- Industry Leading Data Capabilities
- Powerful AI technology
- Patent DNA Extraction
Browse by: Latest US Patents, China's latest patents, Technical Efficacy Thesaurus, Application Domain, Technology Topic, Popular Technical Reports.
© 2024 PatSnap. All rights reserved.Legal|Privacy policy|Modern Slavery Act Transparency Statement|Sitemap|About US| Contact US: help@patsnap.com