Total station instrument and lofting and guiding method thereof
A total station and working method technology, applied in the direction of instruments, surveying instruments, surveying and navigation, etc., can solve the problems of large uncertain position range, short distance, laser safety power limited divergence angle, etc., and achieve high reliability and precision , the effect of convenient process
- Summary
- Abstract
- Description
- Claims
- Application Information
AI Technical Summary
Problems solved by technology
Method used
Image
Examples
Embodiment 1
[0017] like figure 1 , the total station of the present embodiment includes: a driver 12 and a laser 13 connected to the processor unit 11 in turn, the output optical path of the laser 13 is successively provided with a launch optical fiber 14, a collimator for compressing the laser light into a bunch of collimated light Lens 15, reflective element 6 and objective lens 7; reflective element 6 and objective lens 7 have a common central axis, and this central axis is the collimation axis 20 of total station; the rear side of reflective element 6 is coaxially provided with dichroic prism 8, which One side of 8 is provided with image sensor 9, and image sensor 9 is connected with image processor 10, and image processor 10 is connected with processor unit 11; During work, processor unit 11 (preferably ARM processor or computer) is controlled by driver 12 Laser 13 produces laser light, and this laser light passes through emitting fiber 14, collimator lens 15 successively, then passe...
Embodiment 2
[0023] The method of using the total station of the above-mentioned embodiment 1 for lofting guidance includes: erecting the total station in the construction channel, aiming at the direction of the stakeout point or the direction of pipe jacking and then not moving. Fix the reflective prism 100 on the collimation axis, and detect the position of the reflected light spot in the image in real time when the shield machine head is moving, calculate the deviation data between the orientation of the reflective prism 100 and the orientation of the collimation axis 20, and make The deviation data and the image are displayed in real time on the staff's mobile communication device, and the staff adjusts the traveling direction of the shield machine head in real time according to the deviation data and the image, so that the reflective prism 100 returns to the collimation axis , and then make the shield head travel along the collimation axis.
Embodiment 3
[0025] The method for stakeout guidance using the total station of the above-mentioned embodiment 1 includes: during construction stakeout, according to the construction drawing, erecting the total station in the reference station, aiming the total station at the direction of the required stakeout point on the construction drawing and then not moving , the target placement staff moves the reflective target 100 to the collimation axis, the instrument detects the position of the reflected light spot in the image in real time, calculates the deviation data between the orientation of the reflective target 100 and the orientation of the collimation axis 20, and makes The deviation data and the image are displayed in real time on the staff's mobile communication device, and the staff moves the reflective target 100 to the collimation axis of the instrument according to the deviation data and image instructions, and the front and rear distance between the reflective target 100 and the ...
PUM
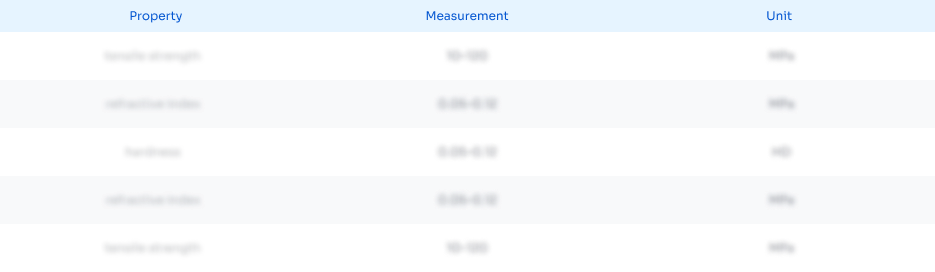
Abstract
Description
Claims
Application Information

- Generate Ideas
- Intellectual Property
- Life Sciences
- Materials
- Tech Scout
- Unparalleled Data Quality
- Higher Quality Content
- 60% Fewer Hallucinations
Browse by: Latest US Patents, China's latest patents, Technical Efficacy Thesaurus, Application Domain, Technology Topic, Popular Technical Reports.
© 2025 PatSnap. All rights reserved.Legal|Privacy policy|Modern Slavery Act Transparency Statement|Sitemap|About US| Contact US: help@patsnap.com