High-temperature and large-range silicon-sapphire pressure sensor structure
A pressure sensor, sapphire technology, applied in the direction of measuring force, instruments, measuring devices, etc., can solve the problems of large measurement range, small measurement range, low sensitivity, etc., and achieve the effect of avoiding p-n isolation and improving the working temperature range
- Summary
- Abstract
- Description
- Claims
- Application Information
AI Technical Summary
Problems solved by technology
Method used
Image
Examples
Embodiment Construction
[0017] The structure of the high-temperature and large-range silicon-sapphire pressure sensor of the present invention will be further described below in conjunction with the accompanying drawings.
[0018] Silicon-sapphire pressure sensor structure of the present invention such as figure 1 As shown, it mainly includes a titanium alloy shell 1, a lower titanium alloy diaphragm 2, a sapphire diaphragm 3, a single crystal silicon strain resistance 4, an upper titanium alloy diaphragm 5, a connecting cylinder 6 and a metal lead 7. Among them, the titanium alloy shell 1 provides support and protection for other components, and the lower titanium alloy diaphragm 2 and the sapphire diaphragm 3 are combined by vacuum sintering to form an elastic sensitive diaphragm; the sapphire diaphragm 3 is used as the substrate, and the On it, the single crystal silicon strain resistance 4 is processed by semiconductor technology to form a silicon-sapphire structure; the single crystal silicon st...
PUM
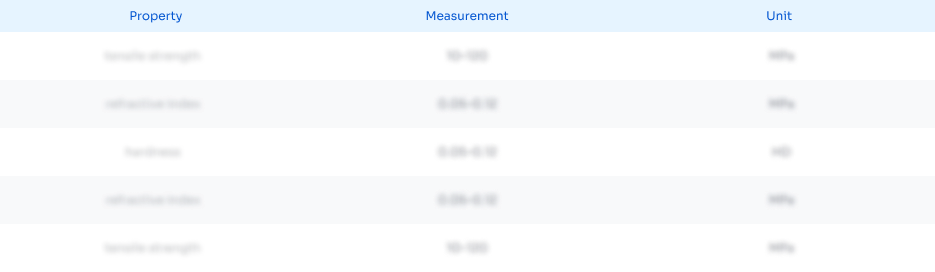
Abstract
Description
Claims
Application Information

- R&D Engineer
- R&D Manager
- IP Professional
- Industry Leading Data Capabilities
- Powerful AI technology
- Patent DNA Extraction
Browse by: Latest US Patents, China's latest patents, Technical Efficacy Thesaurus, Application Domain, Technology Topic, Popular Technical Reports.
© 2024 PatSnap. All rights reserved.Legal|Privacy policy|Modern Slavery Act Transparency Statement|Sitemap|About US| Contact US: help@patsnap.com