Robot remote tool coordinate attitude automatic positioning device and its positioning method
A technology of automatic positioning and tool coordinates, applied in the field of robotics, to achieve the effect of complicated operation steps, saving manpower and time, and improving productivity
- Summary
- Abstract
- Description
- Claims
- Application Information
AI Technical Summary
Problems solved by technology
Method used
Image
Examples
Embodiment approach
[0016] figure 2 Shows an embodiment of the robot remote tool coordinate posture automatic positioning device of the present invention, which includes a first test end 2 installed on the robot flange 1 and a second test installed on the center point of the remote tool 4 Terminal 3. The first test terminal 2 and the second test terminal 3 are connected by a data line 5. The first test terminal 2 is composed of a gyroscope sensor and a laser sensor, and the second test terminal 3 is a gyroscope. The first test terminal 2 and the second test terminal 3 are finally connected to the robot terminal through a data line.
[0017] Its robot remote tool coordinate posture automatic positioning method includes the following steps:
[0018] The first step is to obtain the posture of the center point of the remote tool: first, fix the first test end 2 on the flange of the robot, and fix the second test end 3 on the center point of the remote tool 4 for a while. Then, the robot The posture of ...
PUM
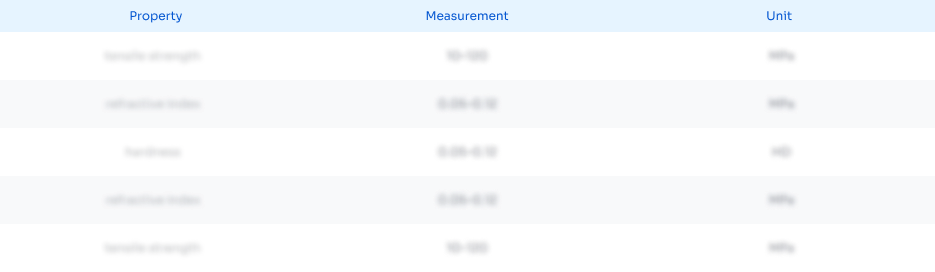
Abstract
Description
Claims
Application Information

- R&D Engineer
- R&D Manager
- IP Professional
- Industry Leading Data Capabilities
- Powerful AI technology
- Patent DNA Extraction
Browse by: Latest US Patents, China's latest patents, Technical Efficacy Thesaurus, Application Domain, Technology Topic, Popular Technical Reports.
© 2024 PatSnap. All rights reserved.Legal|Privacy policy|Modern Slavery Act Transparency Statement|Sitemap|About US| Contact US: help@patsnap.com