Additive manufacturing method for metal-based particle reinforced member
A particle enhancement and additive manufacturing technology, applied in the direction of additive processing, etc., can solve the problems of unfavorable forming, low temperature, low viscosity, etc., to achieve the effect of controlling flow and forming, and solving poor combination
- Summary
- Abstract
- Description
- Claims
- Application Information
AI Technical Summary
Problems solved by technology
Method used
Image
Examples
Embodiment 1
[0019] Embodiment 1: see figure 1 , figure 2 , a method for additive manufacturing of metal-based particle reinforced components, comprising the following steps:
[0020] A. Metal aluminum is melted in a crucible with a nozzle at the bottom, and the heating method is resistance heating; and the temperature is kept above 660°C, and TiC ceramic particles with a particle size of 10 μm that do not chemically react with metal aluminum are added to it, ceramic particles The mass ratio to aluminum is 1:4, and the ceramic particles are evenly distributed in the metal aluminum melt by mechanical stirring, and the metal melting is protected by inert gas;
[0021] B. Set a horizontal base plate and its control equipment for three-dimensional movement under the nozzle. The inner diameter of the nozzle is 2mm, and the distance between the nozzle and the horizontal base plate is 10mm;
[0022] C. Set a predetermined program in the horizontal substrate control device to control the direct...
PUM
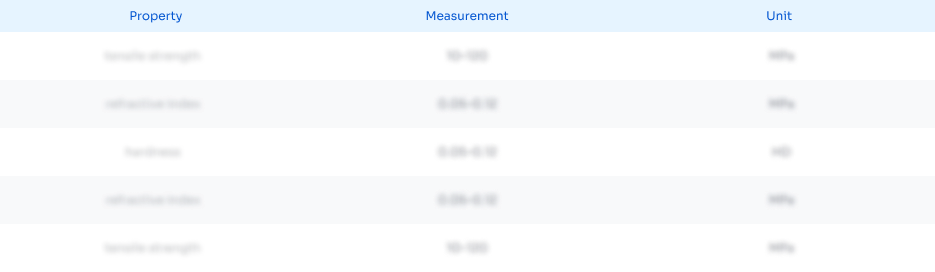
Abstract
Description
Claims
Application Information

- R&D
- Intellectual Property
- Life Sciences
- Materials
- Tech Scout
- Unparalleled Data Quality
- Higher Quality Content
- 60% Fewer Hallucinations
Browse by: Latest US Patents, China's latest patents, Technical Efficacy Thesaurus, Application Domain, Technology Topic, Popular Technical Reports.
© 2025 PatSnap. All rights reserved.Legal|Privacy policy|Modern Slavery Act Transparency Statement|Sitemap|About US| Contact US: help@patsnap.com