Automobile side body outer plate mould with double-layer sliding block structure
A technology for the outer panel and the automobile side, which is applied in the field of automotive side panel outer panel molds, can solve the problems of occupying a stamping workshop, large mold dimensions, and high cost of mold tooling, saving occupied area, meeting precision requirements, and reducing The effect of development costs
- Summary
- Abstract
- Description
- Claims
- Application Information
AI Technical Summary
Problems solved by technology
Method used
Image
Examples
Embodiment Construction
[0015] specific implementation plan
[0016] The present invention will be further described in detail below through specific embodiments in conjunction with the accompanying drawings.
[0017] like figure 1 Shown: the automobile side wall outer panel mold of the present invention comprises upper formwork 5, lower formwork 6, binder plate 1, upper formwork 5 is provided with downward drive wedge 8, and lower formwork is provided with thrust block 7, stop The push block is provided with a guide plate 4, and the lower formwork is provided with an intermediate over-slope 10, on which a return spring 12 is provided, and a slide plate 11 is provided at the bottom, and a guide plate 9 is provided at the corresponding position of the drive slant 8, and an over-slope is provided in the middle. The top of wedge 10 is provided with up and down motion slide block 13, and one side is provided with slide plate 14, and top is provided with return spring 15, is provided with flanging convex...
PUM
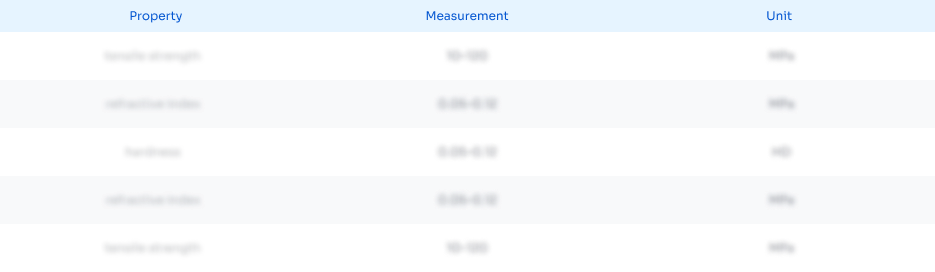
Abstract
Description
Claims
Application Information

- R&D
- Intellectual Property
- Life Sciences
- Materials
- Tech Scout
- Unparalleled Data Quality
- Higher Quality Content
- 60% Fewer Hallucinations
Browse by: Latest US Patents, China's latest patents, Technical Efficacy Thesaurus, Application Domain, Technology Topic, Popular Technical Reports.
© 2025 PatSnap. All rights reserved.Legal|Privacy policy|Modern Slavery Act Transparency Statement|Sitemap|About US| Contact US: help@patsnap.com