Prefabricated composite shell mould built-in prestressed steel reinforced concrete wall
A concrete wall and prestressing technology, applied to walls, building components, buildings, etc., can solve the problems of damage and waste of wooden formwork, affect the progress of the project, and require a large amount of labor for wall masonry, so as to reduce the amount of use and reduce fire hazards , the effect of shortening the time
- Summary
- Abstract
- Description
- Claims
- Application Information
AI Technical Summary
Problems solved by technology
Method used
Image
Examples
Embodiment 1
[0039] Embodiment 1 has insulation layer for the present invention: (as figure 1 , 3 , 4, 5-14)
[0040] A prefabricated laminated formwork with a built-in prestressed steel concrete wall, the prestressed steel 1 is placed in the air in the prefabricated thermal insulation laminated formwork 2, and the concrete wall is formed after pouring concrete 5;
[0041] The prestressed section steel 1 is composed of prestressed tendons 6, section steels 7 and end plates 8, and is used as wall stress tendons;
[0042] The two ends of the prestressed tendon shaped steel 1 are end plates 6, and shaped steel 7 and prestressed tendons 8 are inserted in the end plate 6, the prestressed tendons 8 are located at the outer edge of the end plate 6, and the shaped steel 7 is located in the middle of the end plate 6;
[0043] The thermal insulation laminated formwork is divided into two parts, the outer leaf plate and the inner leaf plate, and the outer leaf plate is equipped with an insulating p...
Embodiment 2
[0053] Embodiment 2 is that the present invention does not have insulation layer: (as figure 2 , 5 -14)
[0054] A prefabricated laminated formwork with a built-in prestressed steel concrete wall, the prestressed steel 1 is placed in the air in the prefabricated thermal insulation laminated formwork 2, and the concrete wall is formed after pouring concrete 5;
[0055] The prestressed section steel 1 is composed of prestressed tendons 6, section steels 7 and end plates 8, and is used as wall stress tendons;
[0056] The two ends of the prestressed tendon shaped steel 1 are end plates 6, and shaped steel 7 and prestressed tendons 8 are inserted in the end plate 6, the prestressed tendons 8 are located at the outer edge of the end plate 6, and the shaped steel 7 is located in the middle of the end plate 6;
[0057] The thermal insulation laminated formwork is divided into two parts, the outer leaf plate and the inner leaf plate, and the truss reinforcement 4 is arranged inside...
PUM
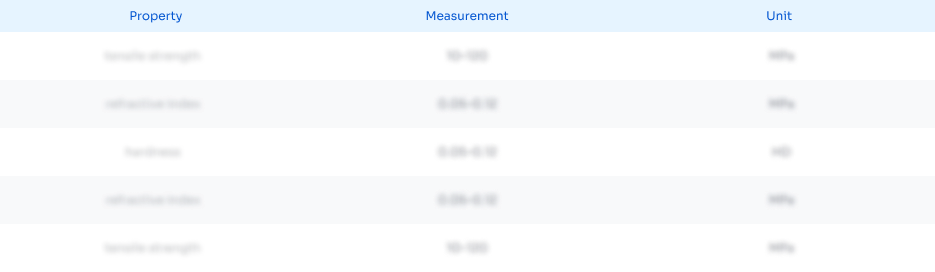
Abstract
Description
Claims
Application Information

- Generate Ideas
- Intellectual Property
- Life Sciences
- Materials
- Tech Scout
- Unparalleled Data Quality
- Higher Quality Content
- 60% Fewer Hallucinations
Browse by: Latest US Patents, China's latest patents, Technical Efficacy Thesaurus, Application Domain, Technology Topic, Popular Technical Reports.
© 2025 PatSnap. All rights reserved.Legal|Privacy policy|Modern Slavery Act Transparency Statement|Sitemap|About US| Contact US: help@patsnap.com