Finished product annealing process for double zero aluminum foils
A double-zero aluminum foil and finished product annealing technology, which is applied in the processing field of aluminum foil, can solve the problems of poor adhesion, reduce the mechanical properties of aluminum foil, and low annealing efficiency, and achieve remarkable results, speed up the oil removal rate, and improve the annealing efficiency.
- Summary
- Abstract
- Description
- Claims
- Application Information
AI Technical Summary
Problems solved by technology
Method used
Examples
Embodiment 1
[0023] The double-zero aluminum foil described in this implementation is an A1235 / 8079 alloy double-zero aluminum foil, and its finished annealing process includes the following steps: a, standing outside the furnace, b, pretreatment in the furnace, c, slow heating, d, medium temperature annealing, e, low temperature annealing, f, cooling in the furnace, g, air cooling out of the furnace;
[0024] The step of standing outside the furnace is to place the aluminum foil in the area to be annealed for 12 hours, so that the stress of the aluminum foil during the production process is released and tends to be balanced;
[0025] The pretreatment step in the furnace is to place the double-zero aluminum foil in front of the furnace 24 hours in advance before putting it into the furnace, and manually start the cycle, purge, and negative pressure fan (conventional technology) in the box-type annealing furnace to make the double-zero aluminum foil and The atmosphere in the furnace is cons...
Embodiment 2
[0033] The double-zero aluminum foil described in this implementation is an A1235 / 8079 alloy double-zero aluminum foil, and its finished annealing process includes the following steps: a, standing outside the furnace, b, pretreatment in the furnace, c, slow heating, d, medium temperature annealing, e, low temperature annealing, f, cooling in the furnace, g, air cooling out of the furnace;
[0034] The step of standing outside the furnace is to place the aluminum foil in the area to be annealed for 20 hours, so that the stress of the aluminum foil during the production process is released and tends to be balanced;
[0035] The pretreatment step in the furnace is to place the double-zero aluminum foil in front of the furnace 28 hours in advance before putting it into the furnace, and manually start the circulation, blowing and negative pressure fan (conventional technology) in the box-type annealing furnace to make the double-zero aluminum foil and The atmosphere in the furnace ...
Embodiment 3
[0042] The double-zero aluminum foil described in this implementation is an A1235 / 8079 alloy double-zero aluminum foil, and its finished annealing process includes the following steps: a, standing outside the furnace, b, pretreatment in the furnace, c, slow heating, d, medium temperature annealing, e, low temperature annealing, f, cooling in the furnace, g, air cooling out of the furnace;
[0043] The step of standing outside the furnace is to place the aluminum foil in the area to be annealed for 28 hours, so that the stress of the aluminum foil during the production process is released and tends to be balanced;
[0044] The pretreatment step in the furnace is to place the double-zero aluminum foil in front of the furnace 35 hours in advance before putting it into the furnace, and manually start the cycle, purge, and negative pressure fan (conventional technology) in the box-type annealing furnace to make the double-zero aluminum foil and The atmosphere in the furnace is cons...
PUM
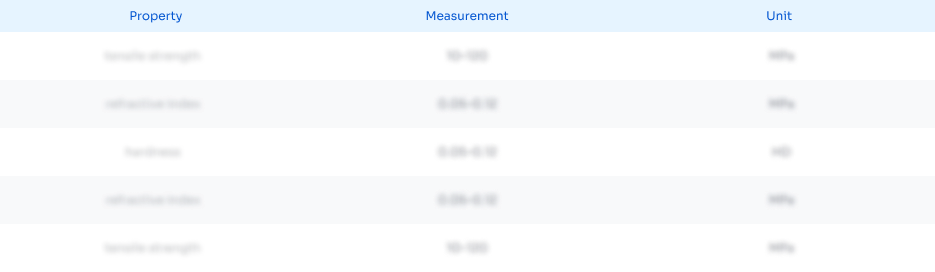
Abstract
Description
Claims
Application Information

- R&D
- Intellectual Property
- Life Sciences
- Materials
- Tech Scout
- Unparalleled Data Quality
- Higher Quality Content
- 60% Fewer Hallucinations
Browse by: Latest US Patents, China's latest patents, Technical Efficacy Thesaurus, Application Domain, Technology Topic, Popular Technical Reports.
© 2025 PatSnap. All rights reserved.Legal|Privacy policy|Modern Slavery Act Transparency Statement|Sitemap|About US| Contact US: help@patsnap.com