High-strength 2024 aluminum alloy thin-wall angle profile production process
A production process and aluminum alloy technology, which is applied in the field of aluminum alloy, can solve the problems of low yield and production efficiency, and achieve the effects of increasing yield, improving dimensional accuracy, and reducing profile deformation
- Summary
- Abstract
- Description
- Claims
- Application Information
AI Technical Summary
Problems solved by technology
Method used
Image
Examples
Embodiment 1
[0032] Such as figure 1 As shown in the production process flow, the production process of a high-strength 2024 aluminum alloy thin-walled corner profile provided by the present invention includes the following steps:
[0033] (1) Structure the mold, that is, add a diversion structure in the extrusion groove of the mold;
[0034] (2) Homogenize the cast rod, that is, the homogenization temperature is 485℃, and the time is 22h;
[0035] (3) Hot extrusion of the cast rod, that is, the homogenized cast rod is preheated to 410°C, 450°C and 445°C before extrusion, and the casting rod is preheated to 450°C and 445°C. The exit speed of the middle profile extrusion can be increased to 0.8m / min;
[0036] (4) The profile is stretched, that is, the profile after hot extrusion is clamped into the stretching device and stretched, and the stretch elongation is 1%;
[0037] (5) Quench and heat the profile, that is, send the stretched profile to the vertical quenching device and perform quenching heat...
Embodiment 2
[0044] The difference between this embodiment and embodiment 1 is that in step 2), the homogenization treatment temperature is 495°C, and the time is 28 hours; in step 3), the casting rod, the mold and the extrusion cylinder are respectively treated before extrusion. Preheat to 415°C, 455°C and 450°C, and during extrusion, the extrusion exit speed of the profile can be increased to 0.9m / min; in step 4), the tensile elongation is 1.2%; in step 5) In step 6), the quenching temperature is 465°C; in step 6), the tensile elongation is 0.4%; and immediately after shaping, and after the straightening is completed, the clamping parts at both ends of the profile are cut off, leaving the middle part. By adopting the above solution, the present invention can increase the extrusion efficiency of the angle profile to 0.9 m / min, and the degree of grain refinement is relatively high.
Embodiment 3
[0046] The difference between this embodiment and the above-mentioned embodiment is: in step 2), the homogenization treatment temperature is 490°C, and the time is 25h; in step 3), the casting rod, the mold and the extrusion cylinder are respectively treated before extrusion. Preheat to 420°C, 460°C and 460°C, and during extrusion, the extrusion exit speed of the profile can be increased to 1.0m / min; in step 4), the tensile elongation is 1.5%; in step 5) In step 6, the quenching temperature is 470°C; in step 6), the tensile elongation is 0.5%; and immediately after shaping, and after the straightening is completed, cut off the clamping parts at both ends of the profile, leaving the middle part; in step 7 ) Before, the profiles were also subjected to artificial aging treatment, that is, the stretched and straightened profiles were loaded into an aging furnace with a circulating hot air device and two-stage artificial aging was carried out. The temperature of the first stage was 2...
PUM
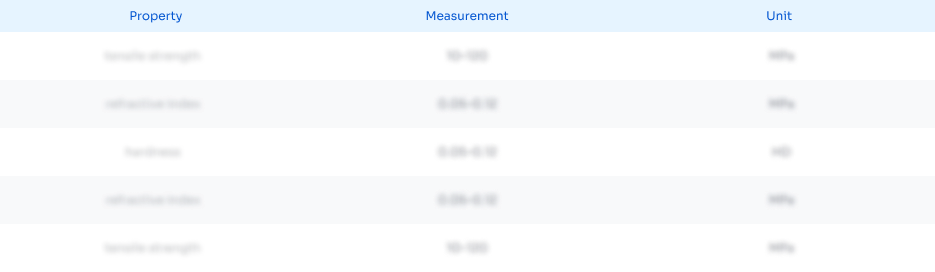
Abstract
Description
Claims
Application Information

- R&D
- Intellectual Property
- Life Sciences
- Materials
- Tech Scout
- Unparalleled Data Quality
- Higher Quality Content
- 60% Fewer Hallucinations
Browse by: Latest US Patents, China's latest patents, Technical Efficacy Thesaurus, Application Domain, Technology Topic, Popular Technical Reports.
© 2025 PatSnap. All rights reserved.Legal|Privacy policy|Modern Slavery Act Transparency Statement|Sitemap|About US| Contact US: help@patsnap.com