Stress relaxation effect considered method and device for evaluating creep-fatigue life of high temperature component
A technology for stress relaxation and high temperature components, which is applied in the field of creep fatigue life evaluation methods and evaluation devices for high temperature components, which can solve the problems of complex calculation of multi-axis correction factors, not recommended, and inability to guarantee stress history.
- Summary
- Abstract
- Description
- Claims
- Application Information
AI Technical Summary
Problems solved by technology
Method used
Image
Examples
Embodiment Construction
[0048] The present invention will be described in detail below in conjunction with the accompanying drawings and specific embodiments. Note that the aspects described below in conjunction with the drawings and specific embodiments are only exemplary, and should not be construed as limiting the protection scope of the present invention.
[0049] In the present invention, a calculation strategy combining finite element calculation and equal strain relaxation model is adopted. First, a certain number of load cycles are calculated by using the thermoelastic creep finite element until the total strain of each state point at the examination point remains basically unchanged. At this time, use the uniaxial equal strain relaxation model combined with the multiaxial correction coefficient M to calculate the same number of load cycles. By continuously adjusting the multiaxial correction coefficient M, the uniaxial equal strain relaxation model combined with the multiaxial correction coe...
PUM
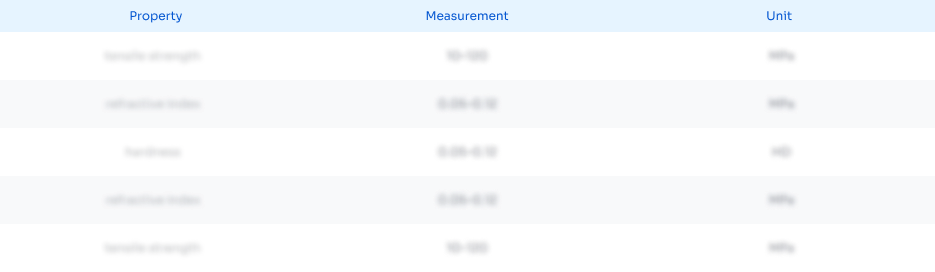
Abstract
Description
Claims
Application Information

- Generate Ideas
- Intellectual Property
- Life Sciences
- Materials
- Tech Scout
- Unparalleled Data Quality
- Higher Quality Content
- 60% Fewer Hallucinations
Browse by: Latest US Patents, China's latest patents, Technical Efficacy Thesaurus, Application Domain, Technology Topic, Popular Technical Reports.
© 2025 PatSnap. All rights reserved.Legal|Privacy policy|Modern Slavery Act Transparency Statement|Sitemap|About US| Contact US: help@patsnap.com