Preparation method for polyfluoromethylpyrazole compound, and intermediate of compound and preparation method thereof
A compound, methyl technology, applied in the field of preparation, intermediates and preparation of polyfluoromethylpyrazole compounds, can solve the problems of low reaction conversion rate, harsh reaction conditions, low reaction yield, etc.
- Summary
- Abstract
- Description
- Claims
- Application Information
AI Technical Summary
Problems solved by technology
Method used
Image
Examples
Embodiment 1
[0127] Add 100g of diethyl malonate (0.625mol) and 315.0g of dehydrated ethanol to the reaction bottle, after completely mixing and dissolving, slowly add the ethanol solution of potassium hydroxide (potassium hydroxide: 35.0 g (0.624mol), ethanol: 315.0g), a white solid was gradually precipitated during the dropwise addition. After the dropwise addition, the reaction solution continued to be stirred at 10-35° C. for about 3.5 hours. Raise the temperature to 79-80°C to reflux the system, then filter while hot to remove dipotassium malonate. The resulting filtrate was cooled to 0°C and filtered to obtain monoethyl malonate potassium salt.
[0128] After the filtrate was concentrated and about 500g of ethanol was further distilled off, the resulting concentrated solution was cooled to 0°C, filtered, and the obtained two parts of monoethyl malonate potassium salt were combined and vacuum-dried to finally obtain 92.06g of monoethyl malonate potassium salt (HPLC purity: 98.8%, yi...
Embodiment 2
[0130] Add 100g of dimethyl malonate (0.757mol) and 350.0g of anhydrous methanol to the reaction flask, after completely mixing and dissolving, slowly add potassium hydroxide methanol solution (potassium hydroxide: 42.3 g (0.754mol), methanol: 350.0g), white solids gradually precipitated during the dropwise addition. After the dropwise addition, the reaction solution continued to be stirred at 10-35° C. for about 3.5 hours. After heating up to 65-68°C to reflux the system, filter while hot to remove dipotassium malonate. The resulting filtrate was cooled to 0°C and filtered to obtain monomethyl malonate potassium salt.
[0131] After the filtrate was concentrated and about 550 g of methanol was further distilled off, the resulting concentrated solution was cooled to 0°C and filtered. After the two parts of monomethyl malonate potassium salt were combined, they were vacuum-dried to obtain 98.78 g of monomethyl malonate potassium salt (HPLC purity: 99.1%, yield: 82.80%).
Embodiment 3
[0133] Add 100g of diethyl malonate (0.625mol) and 315.0g of dehydrated ethanol to the reaction flask, after completely mixing and dissolving, slowly add ethanol solution of sodium hydroxide (sodium hydroxide: 25.0 g (0.624mol), ethanol: 315.0g), and a white solid slowly precipitated out during the dropwise addition. After the dropwise addition, the reaction solution continued to be stirred at 10-35° C. for about 3.5 hours. After heating up to 79-80°C to reflux the system, filter while hot to remove disodium malonate. After about 500 g of ethanol was evaporated from the obtained filtrate, the obtained concentrated solution was cooled to 0° C., filtered, and the obtained monoethyl malonate sodium salt was vacuum-dried to obtain 34.30 g of monoethyl malonate sodium salt (HPLC purity: 98.6%, Yield: 35.12%).
PUM
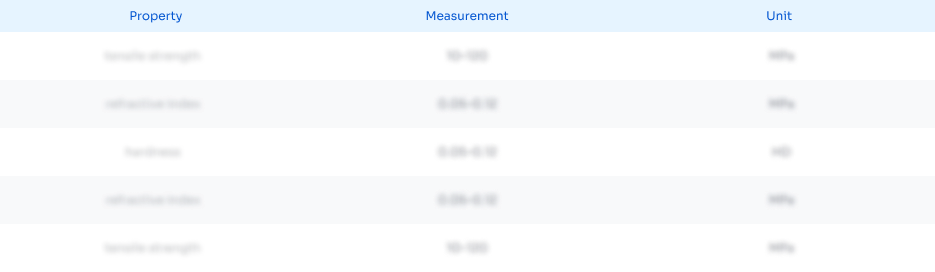
Abstract
Description
Claims
Application Information

- R&D
- Intellectual Property
- Life Sciences
- Materials
- Tech Scout
- Unparalleled Data Quality
- Higher Quality Content
- 60% Fewer Hallucinations
Browse by: Latest US Patents, China's latest patents, Technical Efficacy Thesaurus, Application Domain, Technology Topic, Popular Technical Reports.
© 2025 PatSnap. All rights reserved.Legal|Privacy policy|Modern Slavery Act Transparency Statement|Sitemap|About US| Contact US: help@patsnap.com