Automatic cable returning and winding displacement equipment for optical cable
An automatic and optical cable technology, applied in the direction of light guides, optics, optical components, etc., can solve the problems of low recovery success rate of optical cable sub-units or optical cable sleeves, easy accumulation of cables, clamped and broken tubes, etc., to achieve improved rowing Excellent wire quality, convenient power source, and stable operation
- Summary
- Abstract
- Description
- Claims
- Application Information
AI Technical Summary
Problems solved by technology
Method used
Image
Examples
Embodiment Construction
[0030] In order to make the object, technical solution and advantages of the present invention clearer, the present invention will be further described in detail below in conjunction with the accompanying drawings and embodiments. It should be understood that the specific embodiments described here are only used to explain the present invention, not to limit the present invention. In addition, the technical features involved in the various embodiments of the present invention described below can be combined with each other as long as they do not constitute a conflict with each other.
[0031] refer to figure 1 , figure 2 , an automatic cable unwinding device for an optical cable, comprising a frame 1, a polished rod cable arrangement, a swing arm 3, a tension spring 4, a pressure wheel 5 and a transition guide wheel 7, wherein,
[0032] The polished rod cable arranger includes a cable rotating shaft 2 and a moving body 6 that can reciprocate on the cable rotating shaft 2; ...
PUM
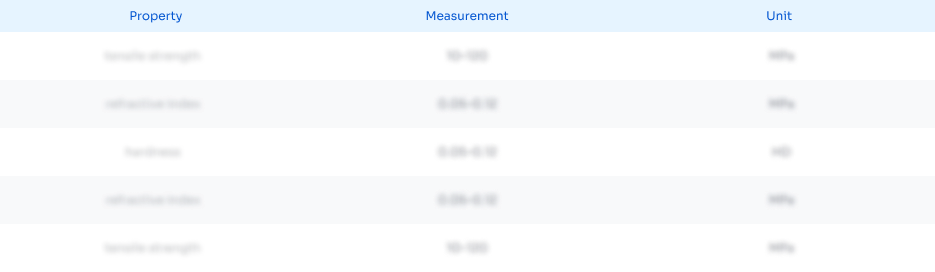
Abstract
Description
Claims
Application Information

- R&D
- Intellectual Property
- Life Sciences
- Materials
- Tech Scout
- Unparalleled Data Quality
- Higher Quality Content
- 60% Fewer Hallucinations
Browse by: Latest US Patents, China's latest patents, Technical Efficacy Thesaurus, Application Domain, Technology Topic, Popular Technical Reports.
© 2025 PatSnap. All rights reserved.Legal|Privacy policy|Modern Slavery Act Transparency Statement|Sitemap|About US| Contact US: help@patsnap.com