Method for improving glossiness of glaze-surface of glazed tile
A technology of glazed tiles and gloss, which is applied in the field of ceramic building decoration materials, can solve the problems of long cycle, long time to adjust the glaze, high production cost, etc., achieve outstanding benefits, improve glaze gloss, and save time
- Summary
- Abstract
- Description
- Claims
- Application Information
AI Technical Summary
Problems solved by technology
Method used
Image
Examples
Embodiment 1
[0035] Specifically, the method for improving glaze glossiness of glazed tiles comprises the following steps:
[0036] 1) Adobe batching ball milling: select adobe raw materials for preparing ceramic glazed tiles, and send the ingredients into a ball mill for ball milling;
[0037] 2) Spray pulverizing and pressing molding: the adobe raw material is spray-dried by a spray drying tower to obtain adobe powder, and the adobe powder is pressed and formed by using the adobe powder to obtain adobe;
[0038] 3) bisque firing: put the brick into a biscuit kiln to burn the biscuit;
[0039] 4) pouring bottom glaze: pouring bottom glaze on the biscuit;
[0040] 5) drenched with smooth glaze: drenched with smooth glaze on the bottom glaze;
[0041] 6) Preparation of gloss-based powder: raw materials include SiO 2 50%, Al 2 o 3 6%, CaO 10%, MgO 2%, K 2 O5%, Na 2 O 0.3%, BaO 1%, B 2 o 3 1%, ZnO 5%, PbO 1%, stir and mix the above-mentioned raw materials according to the proporti...
Embodiment 2
[0048] Specifically, the method for improving glaze glossiness of glazed tiles comprises the following steps:
[0049] 1) Adobe batching ball milling: select adobe raw materials for preparing ceramic glazed tiles, and send the ingredients into a ball mill for ball milling;
[0050] 2) Spray pulverizing and pressing molding: the adobe raw material is spray-dried by a spray drying tower to obtain adobe powder, and the adobe powder is pressed and formed by using the adobe powder to obtain adobe;
[0051] 3) bisque firing: put the brick into a biscuit kiln to burn the biscuit;
[0052] 4) pouring bottom glaze: pouring bottom glaze on the biscuit;
[0053] 5) drenched with smooth glaze: drenched with smooth glaze on the bottom glaze;
[0054] 6) Preparation of gloss-based powder: raw materials include SiO 2 50%, Al 2 o 3 8%, CaO 5%, MgO 2%, K 2 O3%, Na 2 O 0.4%, BaO 1%, B2 o 3 1%, ZnO 5%, PbO 1%, stir and mix the above-mentioned raw materials according to the proportion,...
Embodiment 3
[0062] Specifically, the method for improving glaze glossiness of glazed tiles comprises the following steps:
[0063] 1) Adobe batching ball milling: select adobe raw materials for preparing ceramic glazed tiles, and send the ingredients into a ball mill for ball milling;
[0064] 2) Spray pulverizing and pressing molding: the adobe raw material is spray-dried by a spray drying tower to obtain adobe powder, and the adobe powder is pressed and formed by using the adobe powder to obtain adobe;
[0065] 3) bisque firing: put the brick into a biscuit kiln to burn the biscuit;
[0066] 4) pouring bottom glaze: pouring bottom glaze on the biscuit;
[0067] 5) drenched with smooth glaze: drenched with smooth glaze on the bottom glaze;
[0068] 6) Preparation of sodium-containing glossy glaze layer: put 100 kg of roller printing ink and 10% sodium chloride into a disperser to disperse into flower glaze, and mix to obtain a sodium-containing glossy glaze layer glaze;
[0069] 7) ro...
PUM
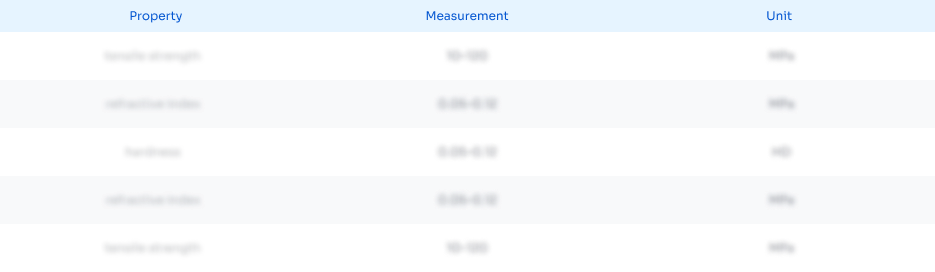
Abstract
Description
Claims
Application Information

- R&D Engineer
- R&D Manager
- IP Professional
- Industry Leading Data Capabilities
- Powerful AI technology
- Patent DNA Extraction
Browse by: Latest US Patents, China's latest patents, Technical Efficacy Thesaurus, Application Domain, Technology Topic, Popular Technical Reports.
© 2024 PatSnap. All rights reserved.Legal|Privacy policy|Modern Slavery Act Transparency Statement|Sitemap|About US| Contact US: help@patsnap.com