Robot joint system
A technology for robot joints and oil supply systems, which is used in manipulators, manufacturing tools, joints, etc.
- Summary
- Abstract
- Description
- Claims
- Application Information
AI Technical Summary
Problems solved by technology
Method used
Image
Examples
Embodiment Construction
[0014] The present invention will be specifically described below in conjunction with the accompanying drawings and embodiments.
[0015] The invention is a robot joint system based on electro-hydraulic direct drive technology.
[0016] figure 1 It is a front view of the overall structure of the present invention.
[0017] figure 2 It is a partially enlarged schematic diagram of the present invention.
[0018] The present invention includes a resonance oil supply system 1, a lower mechanical arm 2, a cylinder piston rod 3, a screw shaft 4, and an upper mechanical arm 5; the resonance oil supply system 1 is composed of a resonance oil supply system 1a and a resonance oil supply system 1b, The resonance oil supply system 1a and the resonance oil supply system 1b are symmetrically and reversely installed inside the lower mechanical arm 2. The lower mechanical arm 2 includes a right oil chamber 2a and a left oil chamber 2b. The oil inlet sleeve 14 of the resonance oil supply s...
PUM
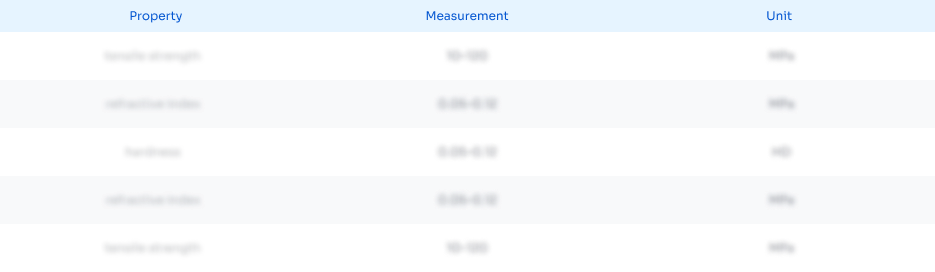
Abstract
Description
Claims
Application Information

- R&D Engineer
- R&D Manager
- IP Professional
- Industry Leading Data Capabilities
- Powerful AI technology
- Patent DNA Extraction
Browse by: Latest US Patents, China's latest patents, Technical Efficacy Thesaurus, Application Domain, Technology Topic, Popular Technical Reports.
© 2024 PatSnap. All rights reserved.Legal|Privacy policy|Modern Slavery Act Transparency Statement|Sitemap|About US| Contact US: help@patsnap.com